The Aramco Hydrocarbon Journey
Refining: Decades of greenhouse gas mitigation in our operational DNA
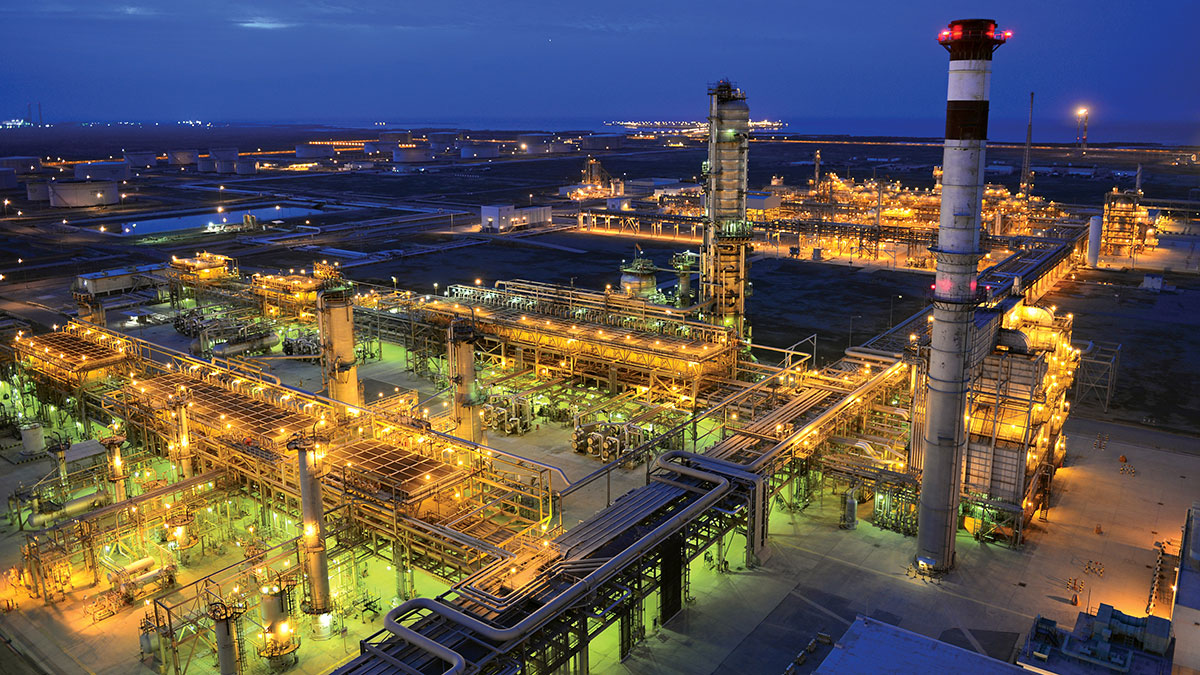
Global December 15, 2021 - By
Refining transforms oil into thousands of useful products, from engine fuels to a variety of household items.
Jazan — Oil’s remarkable versatility shines when it is introduced to the processing intricacies of refining.
Without refining, oil is of mediocre use for modern human lives.
Refining transforms oil into thousands of useful products, from engine fuels to a variety of household items.
Breaking molecular chains
After Aramco hydrocarbons leave the oil field, gas is separated, and the oil is stabilized for delivery to local and joint venture refineries for processing, as well as to terminals for export.
Each refinery is configured differently, and their complexity determines the range of products produced.
Yet, when standing within a refinery, all seem like a giant science lab for manufacturing.
Hydrocarbons — with many different shapes, lengths, weights, and boiling points, are separated from each other according to their molecular chain lengths, and/or types.
Using either natural gravity, heating, cooling, pressure and catalysts, oil refineries crack complex hydrocarbon molecules into simpler and lighter molecules, used to produce premium and high quality products. After the cracking process, some molecules are attached again.
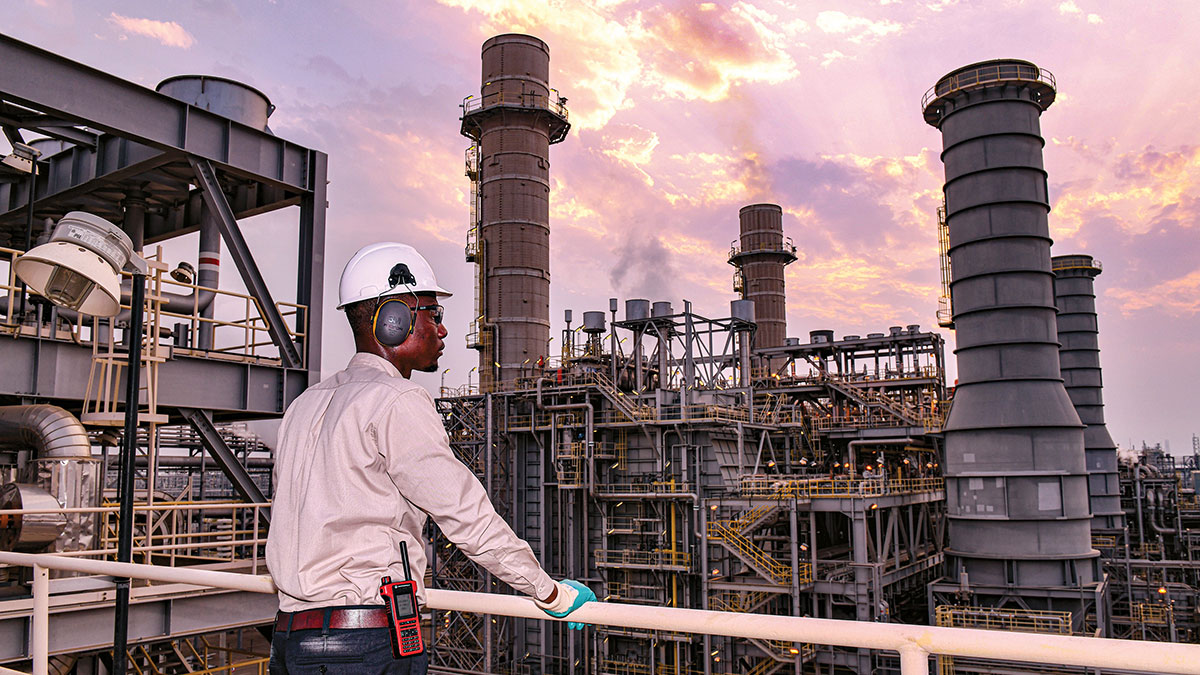
Leading environmental thinking
Aramco’s newly built full conversion Jazan Refinery Complex in the southwest of Saudi Arabia alongside the Red Sea, is currently in final commissioning, and refining at half its full capacity of 400,000 barrels per day.
The 17-km2 strives to maximize the hydrocarbon’s value through production of multiple byproducts within the same facility.
At its simplest, refining oil requires heat and water, and Jazan refinery’s crude distillation unit prepares stabilized Arabian Heavy and Medium crude oil from the Kingdom’s northern oil fields for multiple refining processes by using heat to fractionate the oil into liquefied petroleum gas, naphtha, kerosene, diesel, vacuum gas oil, and vacuum residue.
After sulfur is removed from the naphtha, a continuous catalytic reformer increases its octane rating for use as premium clean fuels, or premium benzene and paraxylene. Sulfur is also removed from both kerosene and diesel to produce cleaner burning fuels.
Molecular chains of the heavier fractions are then cracked down in a hydrocracker to produce more valuable premium products, making the most out of every hydrocarbon.
Refinery plus gas and power
However, smart planning means Jazan refining is far from simple — the refinery is also a gas and power plant, plus it produces petrochemicals.
A green wire fence runs discreetly across the complex’s southern side, separating the refinery from an integrated gasification combined cycle plant (IGCC), one of the world’s largest, and housing a sizable power plant, air separation unit, associated utilities, and what is noted as top technology.
Vacuum residue, oil left at the bottom of the vacuum distillation column, is piped under the fence to the IGCC’s gasification unit, where heat is used to release more gas from the ever-generous hydrocarbons.
In the IGCC, vacuum residue is converted to raw syngas by its complete thermal breakdown into combustible gas in the presence of oxygen and steam — called gasification. This raw syngas, further treated within the IGCC, provides clean syngas to a 3.8 GW five-block combined cycle power plant, producing electricity for both the refinery and the national grid.
Characteristic to multi-producing Jazan, the power plant’s 10 gas and five steam turbines also generate steam for the refinery.
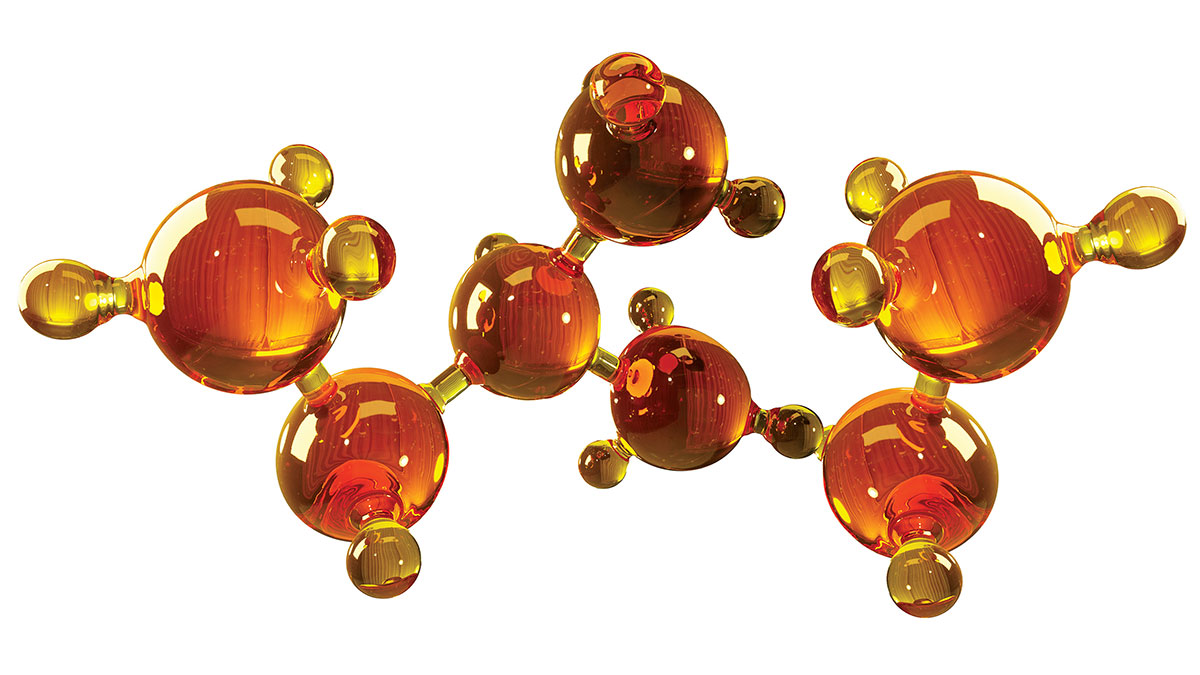
Fewer molecular miles
In addition to the standard refined products of fuel gas, gasoline, and diesel, customers have a lot to choose from at Jazan’s one-stop shop approach: cleaner burning fuels meeting Euro V specs; vanadium and nickel from the dry ash, sulfur, and petrochemical products benzene and paraxylene.
Jazan is the company’s first wholly owned in-Kingdom refinery to produce petrochemicals from naphtha, cutting it into benzene and paraxylene for further outside processing.
Petrochemical manufacturing within the Kingdom directly reduces the imported volumes of raw materials.
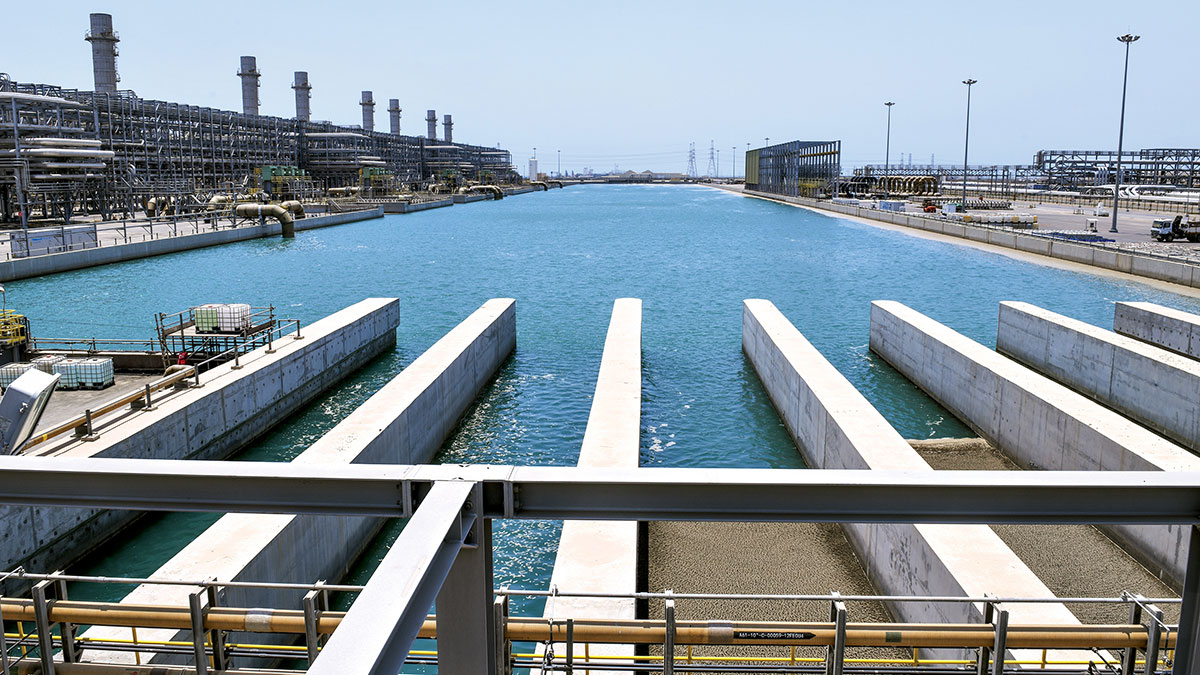
Mesmerizing seawater flow
Processing oil, and generating electricity, requires water, and in Saudi Arabia, a land of no permanent rivers and sparse rainfall, desalination is the region’s lifeblood.
Jazan’s natural rhythm is the adjacent Red Sea, whose cool breezes and teeming seawaters flow in and out of the complex through specially constructed river-like channels, and within nonmetallic pipes, stream into a 43,200 m3/d reverse osmosis desalination plant inside the IGCC, fed by a combination of seawater and treated wastewater.
Reflective of Jazan’s commitment to zero waste, the demineralized water goes for a myriad of uses: boiler feed water, fire water, cooling the power plant, producing steam for refining and other processes, and more.
Operator Abdulmohsen O. Dawshi joined Jazan in 2017, after gaining experience at Yanbu’ refinery and training for 18 months at an Aramco industrial training facility, said, “As a diver, my relationship to the sea is deep and I am proud to work in this plant.”
“Clean production of hydrocarbons is important for the business, the local community, and the planet,” says the west coast local.
A web of front-line barriers and filters prevents marine life from entering the complex through the seawater inlet channel, and the desalination plant’s cooling system ensures a return of waters to the Red Sea.
Not only are the waters treated and returned to a safe temperature by the plant, but a 2.4-km undersea pipe takes the outflow water to a man-made basin into cooler deeper waters, for ultimate temperature mixing with the surrounding waters.
Refining transforms oil into thousands of useful products, from engine fuels to a variety of household items.
Innovative thinking stopping flaring
Imaginative engineering is reducing emissions, saving energy, and more, at Yanbu NGL Fractionation plant.
Natural gas liquids (NGL) produced by gas plants is fed to fractionating plants, where ethane is separated out, and the remaining NGL is fractionated into ethane, propane, butane, and natural gasoline.
At Yanbu’, NGL is received through a 1,170-km pipeline from the Shedgum gas plant.
Any excess ethane at Yanbu’ is stored in liquid form inside an ethane tank for later use.
Vapor pressure building up from liquid ethane requires flaring for safety reasons.
Yanbu’ NGL engineers came up with an idea to not only stop this waste of resource and reduce greenhouse gas emissions compared with flaring operations, but to also use the vapor.
Instead of a typical flare gas recovery system, which requires a gas compressor, the creative Yanbu’ team decided to route the ethane vapor to be used as fuel for the utility plant boilers.
The innovative thinking achieved many benefits: reducing emissions compared to flaring, not wasting resources, and lowering cost.