Global September 01, 2021 - By
Decades of greenhouse gas mitigation in our operational DNA.
Abqaiq wellhead ABQQ-37, resiliently fixed above the Abqaiq oil field, has steadfastly produced crude oil since 1947.
The 74-year-old production warrior may be an elder, but its aboveground assemblage of valves and flanges shine with the freshness of a youngster.
Wellhead ABQQ-37 is testimony to Aramco’s decades-old maintenance diligence for infrastructure — a business model that is good for both the environment, and profitability. Ultimately, well maintained facilities equate to avoidance of greenhouse gas emissions.
Controlling spills and emissions
A hydrocarbon’s processing journey begins when the oil fluids reach the extraction point; the wellhead.
Crude oil fluids — typically comprising oil, dissolved gas, salty water, and some hydrogen sulfide (H2S) — are usually under vast pressure when they reach the surface from the drill hole.
Like a lid on a well-sealed container, wellheads sit above the drill hole’s pipe — a long column of connected pipe cemented to the hole’s sides — bringing control to the natural pressure by sealing the fluids from escaping.
Extraction is when the oil fluids reach the surface from the drill hole, and wellheads stop oil spilling on to the surface, or emitting gas into the atmosphere.
Without wellheads, oil would spill on the surface, and emit gas into the atmosphere. Importantly, wellheads are equipped with an array of valves, all geared toward safety and mitigating greenhouse gas emissions.
Slow and steady is optimal for the flow of crude oil, and choke equipment located downstream of the wellhead, brings steady pressure control to the fluids.
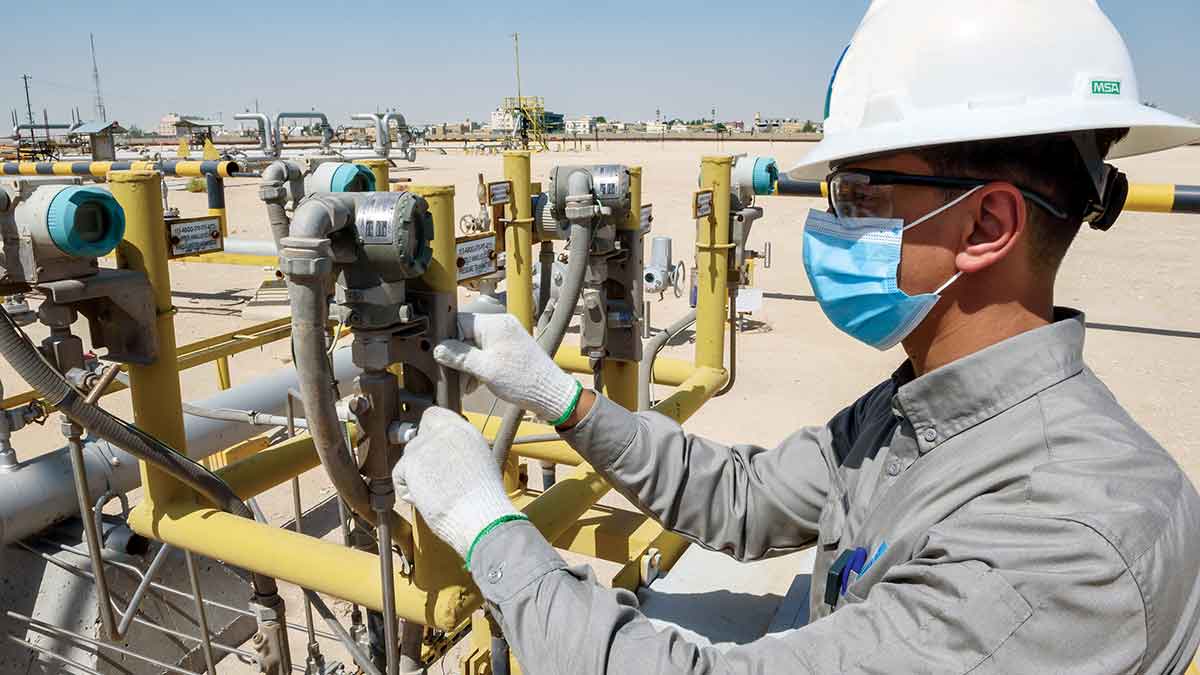
Diligent thoughtful care
The heat of Saudi Arabia’s eastern ad-Dahna desert beats down on Abdalaziz A. Asiri as he grips a shifting spanner to maintain a flange at Wellhead 593.
June to September is hot. Sand storms can block the skid roads, and coat the wellheads. But we have always worked to overcome these issues.
— Abdalaziz A. Asiri
Asiri joined Aramco after finishing school, and has been a field operator ever since — for 10 years — and works for the North Ghawar Producing Department (NGPD), which looks after the Dammam, Abqaiq, and Fazran oil fields, and the northern part of the Ghawar field.
Checking wellheads is central to his role, and important work toward a smooth and low emission arrival of crude oil to the well’s surface.
Protecting people and environment
Wellhead checks include a visual integrity inspection, platform, the electronic sensors, a pressure gauge for the upstream flow line, H2S alarm, choke valve, greasing, tubing casing analysis, testing the master and subsurface safety system, collecting oil samples, and more.
Departing Wellhead 593, which is fenced in to protect fauna and flora, we drive past one of 15 gas-oil separation plants (GOSPs), where water and the majority of dissolved gases are extracted, before the treated oil is fed to the Abqaiq Plants, and gas to Berri and Shedgum.
Asiri explains that regular checks and maintenance of wellheads ensures safety and reliability.
“We check the integrity of all the equipment so the environment and people are protected.”
Abandoned wells, filled with fluid and plugged with cement, are also regularly checked.
Planned desert work
Most of Asiri’s day is spent in the desert. He calls into the office at 7 a.m., receives a job ticket, which he discusses with the supervisor before heading out.
“The production engineer issues instructions to do things like adjusting the choke to adjust the pressure,” said Asiri.
“We cannot be in the desert on our own, so we must register our journey, and travel in a pair.”
For safe and efficient travel, Asiri uses Aramco’s own mobile navigation app for field workers. His journey is monitored through a newly established NGPD field operations support center. Planned remote driving mitigates against impacts on the desert, equates to less energy, maintenance and repair costs — all computing to lower environmental and business costs.
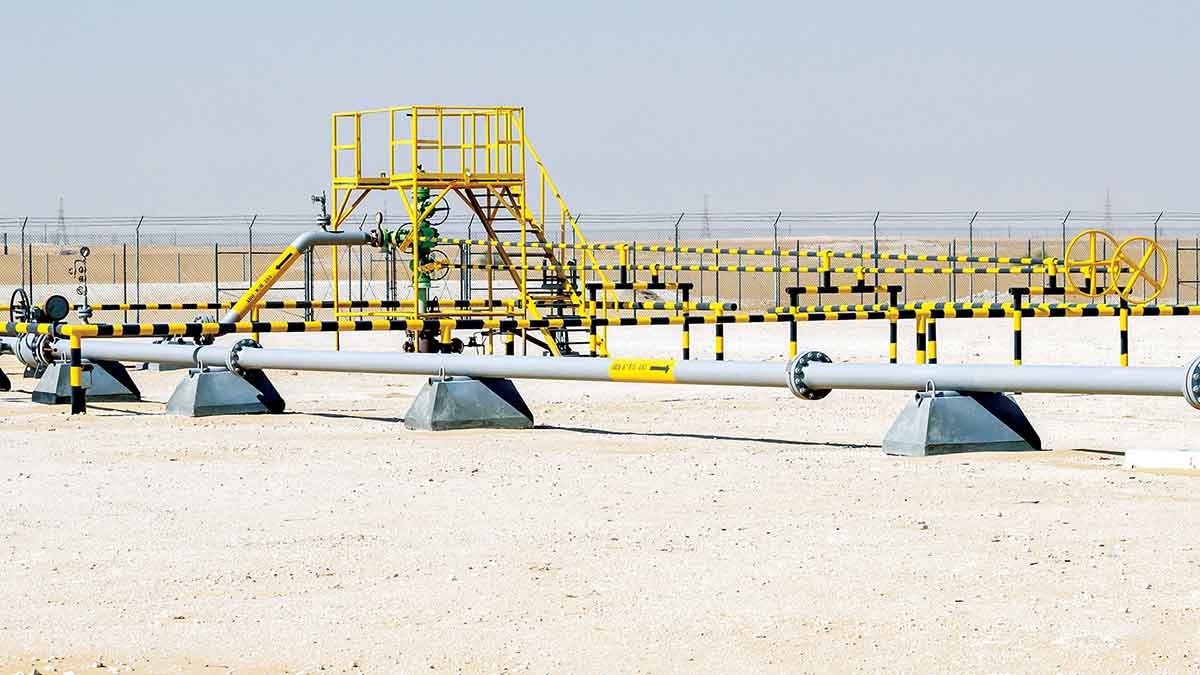
Futuristic modernization
Wellhead 593 sits in the arid industrial heartland of Abqaiq, about 50 km inland from the Arabian Gulf, home to the world’s largest crude oil stabilization facility, and operating for more than seven decades.
Alongside the diligence of ongoing maintenance, there is cutting-edge thinking and technology. Wellheads feed live processing data into a remote terminal unit, which in turn feeds data into nerve centers at the GOSPs.
Through a convergence of software, hardware and communication infrastructure, multitudes of electronic monitoring eyes watch for integrity issues like voids in the piping, tubing or casing, as well as flow parameters.
Energy efficiency are among the improvements at Southern Area Oil Operations (SAOO), whose admin area also spearheaded Aramco’s 1 Million Trees Initiative along with Community Services and Environmental Protection.
Results from tree plantation trials undertaken at SAOO’s Khurais site show water saving irrigation technologies and products to newly planted trees delivered significant reduction in water demand, while positively impacting plant growth.
Prosperity Well
After almost five years of grinding effort, multiple false starts and dashed hopes, a telegram dated March 4, 1938, arrived in San Francisco announcing that Dammam No. 7 was producing at a rate of 1,585 bpd at a depth of 1,440 meters in what would become known as the Arab Zone of porous limestone.
The wellhead made possible the commercial development of oil in Saudi Arabia, and set Aramco firmly on course toward becoming the world’s largest oil producing company. In 1982, after 45 years of near continuous output, Dammam No. 7 was taken out of production.