Aramco Hydrocarbon Journey
Aramco Hydrocarbon Journey: Gas — Decades of greenhouse gas mitigation in our operational DNA
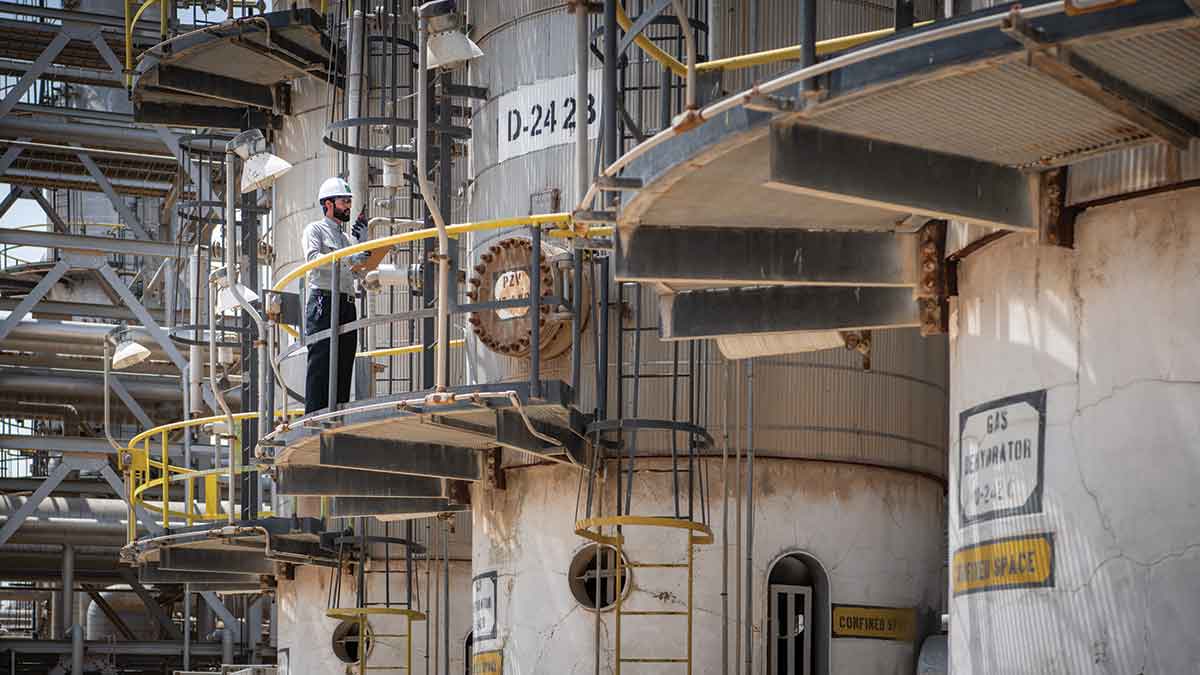
Global November 10, 2021 - By
Gas, at its heart, is a simple hydrocarbon comprising one carbon and four hydrogen molecules, and is found both associated with crude oil, or on its own.
Natural gas, the free-spirited member of the hydrocarbon family, can be hard to pin down.
Of minimal weight, without expert capture inside a pipe, gas will float into the air.
It is also transparent, making it difficult to see.
Gas processing plants prepare gas for direct dispatch to the energy market, and separate natural gas liquids for onward processing at an NGL plant.
Associated and nonassociated
When Aramco crude oil journeys from the field, its associated gas — which was separated from the oil in the gas-oil separation plants and at stabilization facilities — is sent to gas plants.
Willful gas is also found independent of oil.
This nonassociated gas, with its own dedicated gas wells and gathering manifold, is also sent to gas plants for sweetening and fractionation.
Plus, gas likes to play, hiding in tight corners, requiring unconventional methods to entice it to the surface.
Energy transition piece
At its heart, gas is methane — a simple hydrocarbon of one carbon and four hydrogen molecules — and considered an increasingly important piece in the energy mix for the world’s energy transition.
Gas is able to quickly kick-in when intermittent energy sources, like wind and solar, are unable to cover demand.
Aramco’s gas gathering network is strategically located near its fields, reducing transportation, pipeline compression costs, and time to deliver gas products to the market.
Super chilled gas
When sour gas arrives at one of the company’s nine processing plants — Berri, Shedgum, ‘Uthmaniyah, Hawiyah, Haradh, Khursaniyah, Wasit, Midyan, and Fadhili — the collective goal is to condition, sweeten, and then chill the gas to remove its acidic gases (hydrogen sulfide and carbon dioxide), water, and hydrocarbon condensate.
Sweetened gas is ready for direct dispatch to the energy market, while its separated natural gas liquids (NGL) — as one fluid stream — is sent for onward processing at an NGL plant for fractionation into ethane, propane, butane, isobutane, and pentane.
Gas train station
When the Master Gas System was initiated in 1975, Aramco constructed its Berri, Shedgum, and ‘Uthmaniyah gas plants.
Like a central station of an underground train network, Shedgum is a busy, yet mostly quiet, place.
Gas, through a web of underground pipelines, silently snakes its way from southern fields into Shedgum, where it is made ready for its direct onward connection to the domestic energy market, or for the Ju’aymah and Yanbu’ NGL plants.
Receiving equal parts of associated and nonassociated gas, Shedgum is 41 years old, and combines wisdom with innovation to create fresh thinking about gas processing.
Energy efficiency Shedgum priority
Greenhouse gas (GHG) impacts are mitigated when industrial plants become more efficient with their energy use.
To separate the NGL from the light methane gas, its temperature is chilled to a frosty -71 degrees Celsius.
Leaving moisture in gas risks crystallization — known as hydrate formation — which brings an unwanted hazard of pipe blockage.
Removing moisture is the job of the dehydrator system, and to save energy, Shedgum decided to do this differently.
Using a closed loop regeneration cycle, a molecular sieve desiccant is used to capture the moisture, which is dehydrated once it becomes saturated.
Rather than the usual compression of the regeneration gas from 350 psi to 450 psi, the compressors are bypassed, and instead, the desiccant is dehydrated at 350 psi through automated pressurizing and depressurizing of the dehydration columns.
It is achieving the same outcome, without the need for compression.
Supervising operator Eid R. Hajri says stopping the compressors meant reducing power consumption, “Reducing power load also means reducing greenhouse gas emissions.”
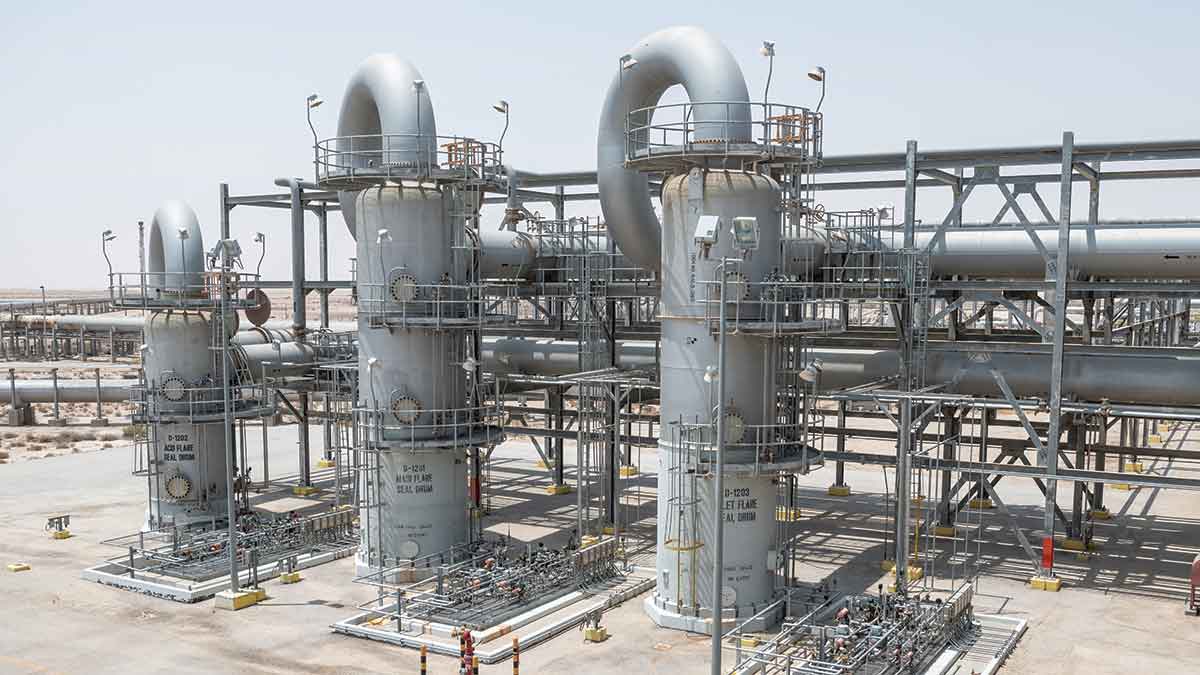
Combatting flaring
One of the infrastructure heroes for reducing GHG emissions are flare gas recovery systems, which are specialized compression systems that recover and repurpose gas that would have previously been flared.
Hajri says Shedgum’s flare recovery infrastructure is one of the company’s larger systems, “Instead of flaring gas, it is sent back into the production facility for production.”
Gas from Shedgum’s flare networks is taken to one of three liquid seal drums, where a water sealing concept recovers gas, and two compression trains then redirect the gas back into the main processing plant.
Hajri has worked at Shedgum for 12 years, and says recovering waste gas is better for the environment.
“People are concerned about climate change, and a closed gas processing system is better for the environment and safety,” said Hajri.
Aramco is a signatory to the World Bank’s “Zero Routine Flaring by 2030” initiative to eliminate routine flaring by 2030, and seeks, over time, to develop an integrated global gas portfolio, and plans to expand its gas business to meet the large and growing domestic demand for low-cost cleaner energy by increasing production, and investing in additional infrastructure.
Gas terms
Raw: Gas prior to processing
Wet: Contains moisture/water
Dry: Contains no moisture/water
Sweet: Minimal treatment as no hydrogen sulfide present
Sour: Hydrogen sulfide is present
Lean: No liquid hydrocarbons require removal
Rich: Contains liquids such as ethane, propane, or butane
Sales: Gas after processing
Natural Gas Liquids (NGL): Heavier hydrocarbons extracted from gas for use as a feedstock in chemical plants
Liquefied Petroleum Gas (LPG): A mix of propane and butane gases with a variety of uses.
Master Gas System: Catch and utilize
The Shedgum sales gas compressor pushes sales gas on its onward underground journey beneath desert sands to the Master Gas System, an extensive network of pipelines collecting natural gas produced in the Kingdom, for distribution to domestic power generation, and other end users.
Capturing and utilizing gas as a source of energy significantly lightened both the Kingdom’s and Aramco’s footprint.
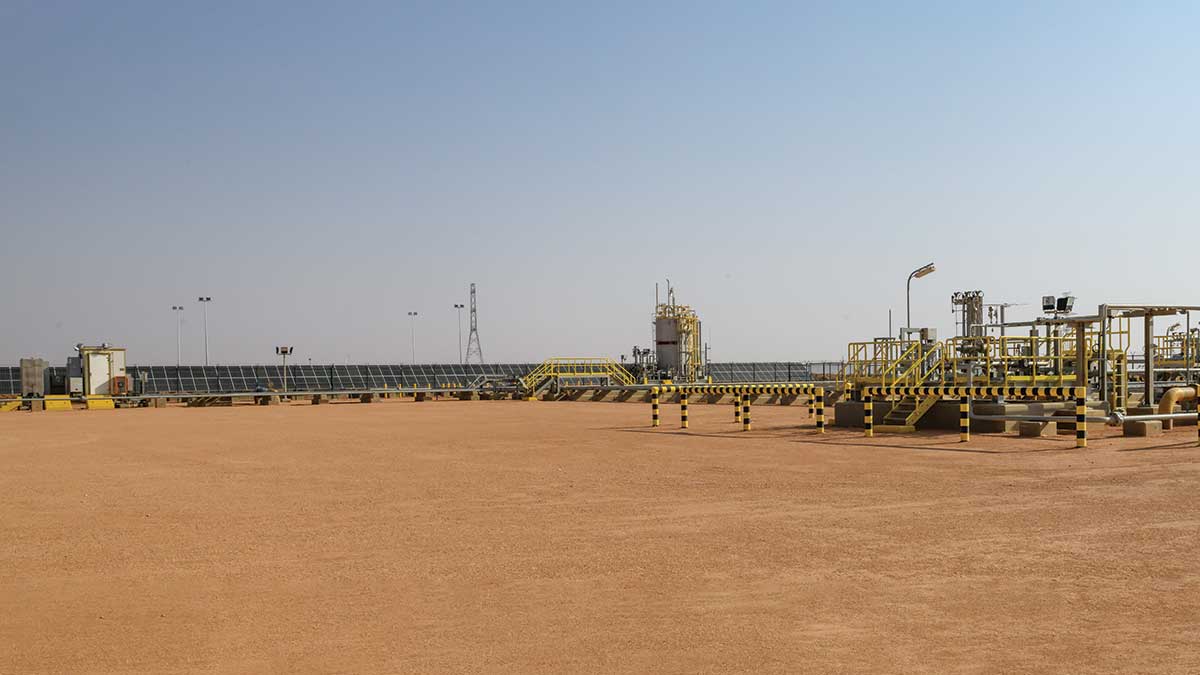
Releasing tight gas
The circular economy makes big turns in the Kingdom’s northern horizon.
North Arabia’s unconventional gas, proudly stubborn, will not come to you. Instead, this tight gas demands you go to it.
Rather than one centralized processing facility, five small dispersed satellite processing facilities (SPF) covering more than 10,000 km2 of the North Arabia field extract the gas, and the facilities’ modular design means they can be moved for continual reuse.
Eleven out of SPF’s 50 wells are powered by solar panels, and from the wells, the gas journeys through nonmetallic piping to the SPF where it is dehydrated to deliver cleaner fuel to power the whole Wa’ad Al Shamal Industrial City.