Global October 19, 2021 - By
Decades of greenhouse gas mitigation in our operational DNA.
Glinting quietly on the skyline of Saudi Arabia’s eastern ad-Dahna desert is a metallic silhouette of assembled pipes, spheroids, columns, vessels, and tanks.
The industrial spot has risen on the desert’s horizon for more than seven decades, and within it, stands the world’s largest crude oil stabilization facility, Abqaiq Plants.
From far-off distances, treated crude propelled by emissions-free gravitational pressure, and some pumping assistance, flows through an extensive network of pipelines into the plant’s massive engineering marvels.
At Abqaiq, people, technology, and a history going back to 1947, fuse together to shape a thoroughly modern stabilization heartland. Deep industrial roots have seeded a thinking operational culture, and high on the precinct’s thoughtful list are actions toward an even lighter environmental footprint.
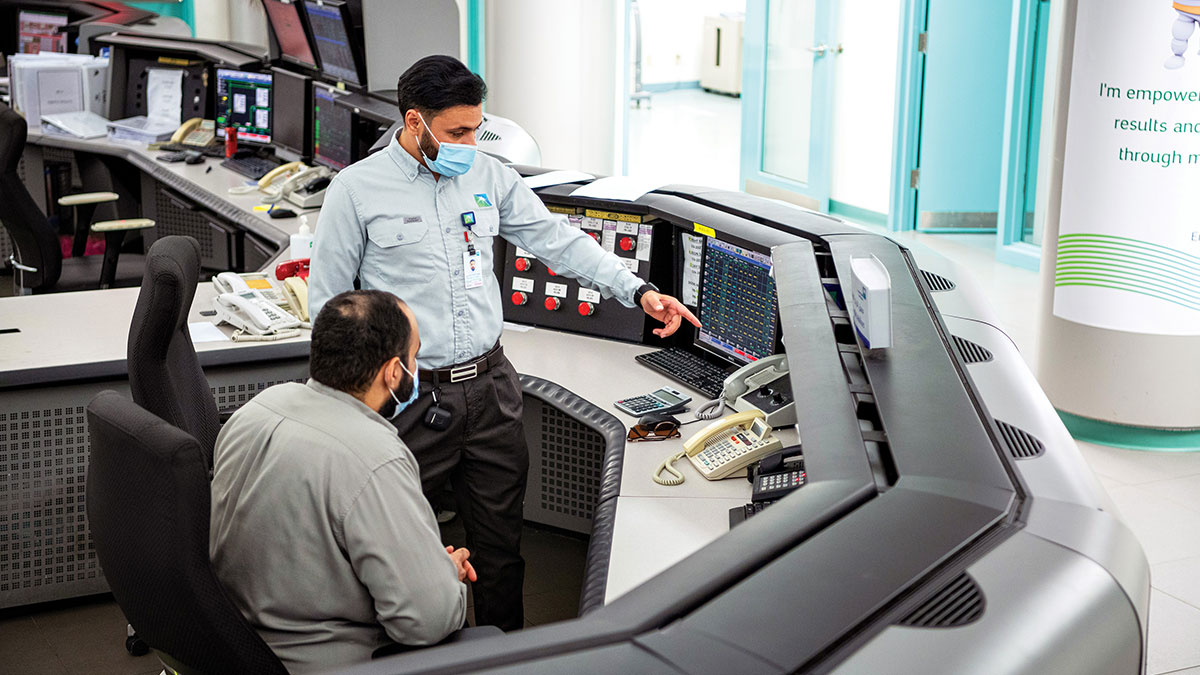
Keeping customers happy
When treated crude — oil from a gas-oil separation plant — flows into Abqaiq, it is still mixed with various kinds of light and sour gases.
Stabilization not only separates these gases from the oil for safe piping, but also prepares the oil to meet Aramco’s customers’ specified requirements.
Three giant facilities at Abqaiq — oil processing, natural gas liquids (NGL), and utilities — work together to stabilize oil, and capture its valuable associated gases for useful products.
Stabilized oil is piped on to Ras Tanura and Jubail on the East Coast, and Yanbu’ in the west, while the light gases go for further processing at other Aramco plants, and the NGL is sent to Ras Tanura.
Stabilization separates more gases from treated crude, allowing for safe handling and shipping, as well as preparing oil to meet specified customer requirements.
Human and machine team up
Humming silently around Abqaiq’s towering steel forest is smart collaborative thinking by both people and technology.
It takes exceptional teamwork to operate an oil and gas facility, and technology is welcomed as a member on the team.
Alongside Abqaiq’s workforce, data provides a helping hand to enhance safety, efficiency, and importantly, mitigate greenhouse gas (GHG) emissions.
At the “Ghawar Intelligence Center” inside Abqaiq’s main administration building, artificial intelligence sensors, advanced analytics, and machine learning click together to present a digital summary across all Aramco’s Southern Area Oil Operations (SAOO).
Gathering all SAOO data together means figuring out strategic actions for energy efficiency, and flaring mitigation.
Analysis, like safely running one pump instead of two, collectively add up to big reductions in GHG emissions, and financial costs.
Clicking on mitigation
Abqaiq’s oil processing facility’s spheroids and stabilizer columns use gravity, heat, and compression to complete final gas separation, while the NGL facility compresses gas in compression trains, and passes it through stripper and deethanizer columns.
It is an intricate process, closely watched 24/7 by both digital and human eyes. Outside operators work one of three shifts, and every shift, take content samples from each oil and NGL process.
A predictive Aramco algorithm uses data from on-site lab analysis samples to automatically adjust multiple process parameters to maximize energy efficiency. In real-time, the advanced process controls also detect any energy abnormality, pinpoint root causes, and advise corrective action.
Within the site’s Distributed Control System building, operators monitor 24/7 how well technology is implementing the algorithm’s techniques.
“The algorithm may decide less steam is required to stabilize a particular oil,” says supervising operator Mohammad A. Zahrani.
“Using less steam means less energy, and less energy means a lower environmental footprint,” adds Zahrani, who has worked at Abqaiq Plants for 23 years.
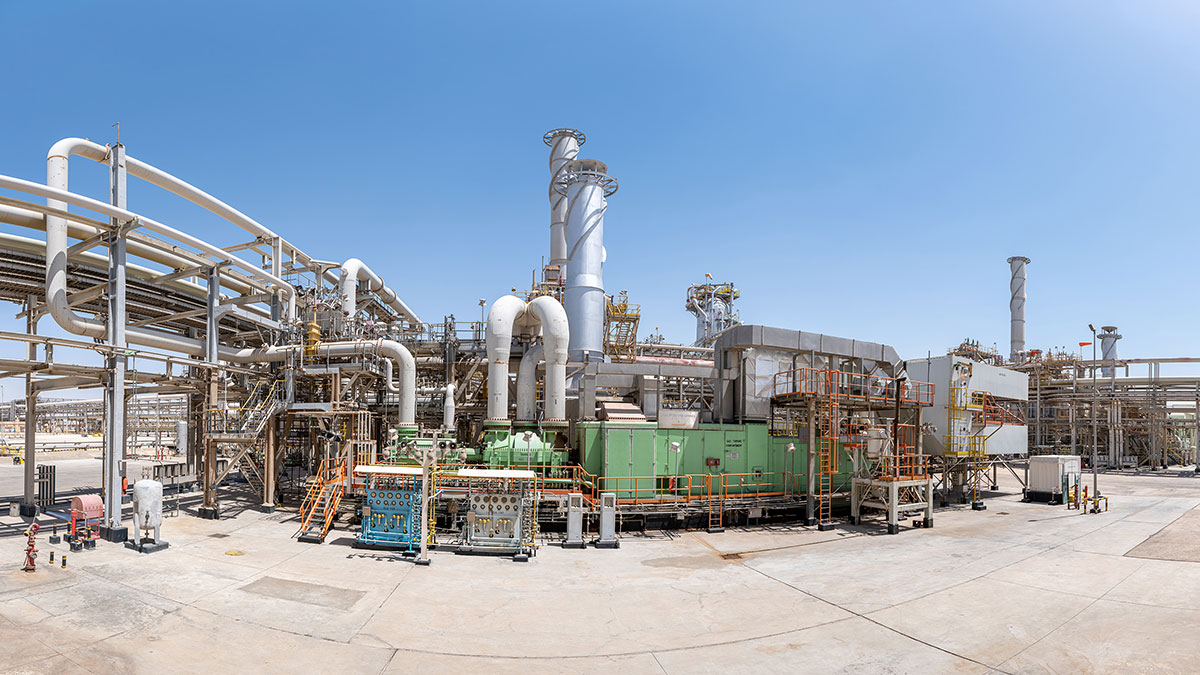
More with less
It takes energy to make energy, and Abqaiq’s power comes mainly from the utility facility’s three generators. The facility also supplies steam, treated water from 16 reverse osmosis units, and instrument air — used to control valves — from two steam-driven and three motor-driven compressors.
Lowering energy intensity — a measure of how much energy a facility consumes to meet its production requirements — at industrial facilities like Abqaiq has a big energy conservation impact, and since 2015, the site has improved its energy intensity by 20%.
Upgrading older equipment can enhance their efficiency. One of the site’s NGL combustion gas turbine drivers is currently being replaced with a new steam compression train. The significant switch means steam, rather than gas, will primarily fuel the turbine, bringing substantive reduction in energy consumption and GHG emissions.
“Abqaiq Plants has operated for many years next to the Abqaiq community, where our families and friends live,” Zahrani noted.
“It is our responsibility to take care of the plant to always make sure we operate safely, and this is best for people and the environment.”
Using wasted heat
Unused energy is a waste of precious resources, and Abqaiq’s cogeneration system captures the most out of every consumed cubic foot of gas.
Gaining the best thermal efficiency from cogeneration requires monitoring of the fuel supply, and ambient temperature.
“We achieve optimum efficiency with Abqaiq’s cogeneration system,” says supervising operator Mohammad A. Zahrani. “All the manufacturer’s upgrades are put into our cogeneration systems, and we particularly watch its operation during late summer when our foggy weather can make them sensitive.”
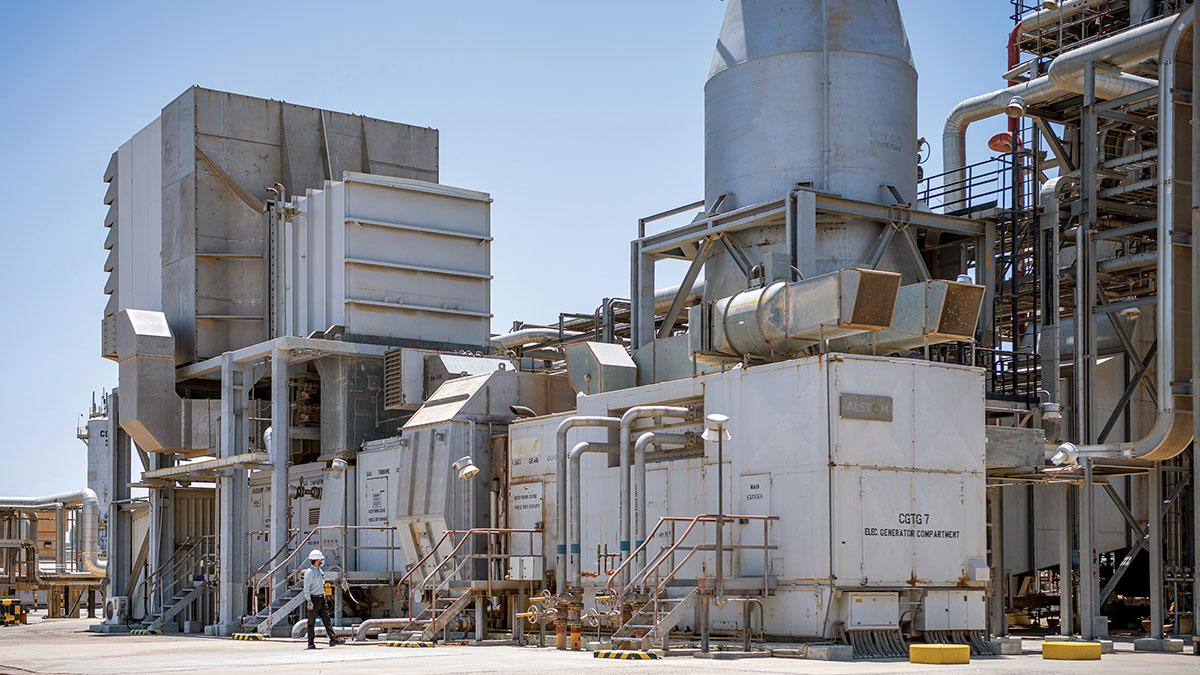
Aramco methane among lowest
In the Abqaiq Plants cogeneration plant, supervising operator Mohammad A. Zahrani uses a hand-held methane analyzer to check for possible leaks of methane and volatile gases.
Natural gas, a lower carbon energy source, consists primarily of methane, which is just one carbon molecule surrounded by four hydrogen molecules (CH₄).
Control of fugitive methane emissions requires thoughtful expertise as its global warming potential is significantly higher than that of carbon dioxide.
At Abqaiq, a drone, methane analyzer, MX4 gas detector, and low emission level sensors are being used to detect and quantify methane emissions.
With a 2020 upstream methane intensity of 0.06%, Aramco’s upstream methane emissions intensity is among the lowest in the industry.
Flaring minimization
Flaring is a safety mitigation activity, burning off gases to maintain proper pressure.
As far back as the 1970s, Aramco introduced a program to significantly reduce the amount of gas the company flares.
Abqaiq Plants has two elevated flares, and like all Aramco facilities, its flare system is connected to the company’s corporate flaring monitoring system at the Dhahran headquarters, where all flaring events are measured and monitored.
Abqaiq flares are equipped with assisted smokeless flare tip technology, which helps mitigate emissions even further.
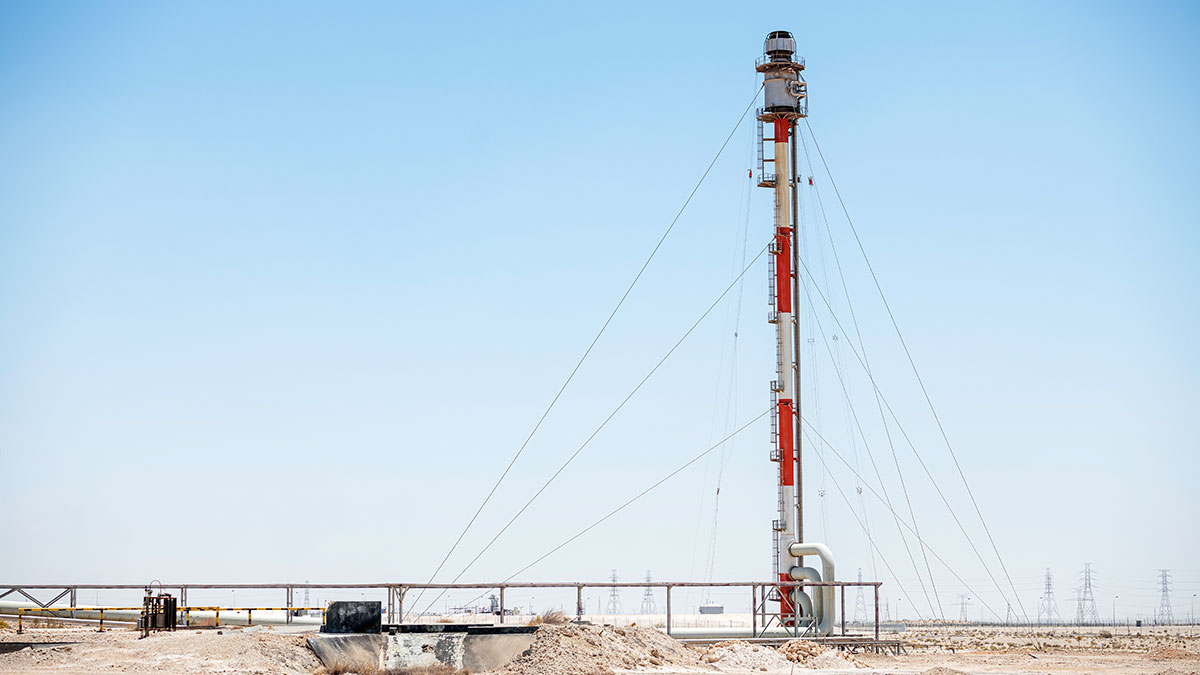