Gas Portfolio
Investing to grow our gas portfolio: Haradh and Hawiyah increment (Story 2 of 2)
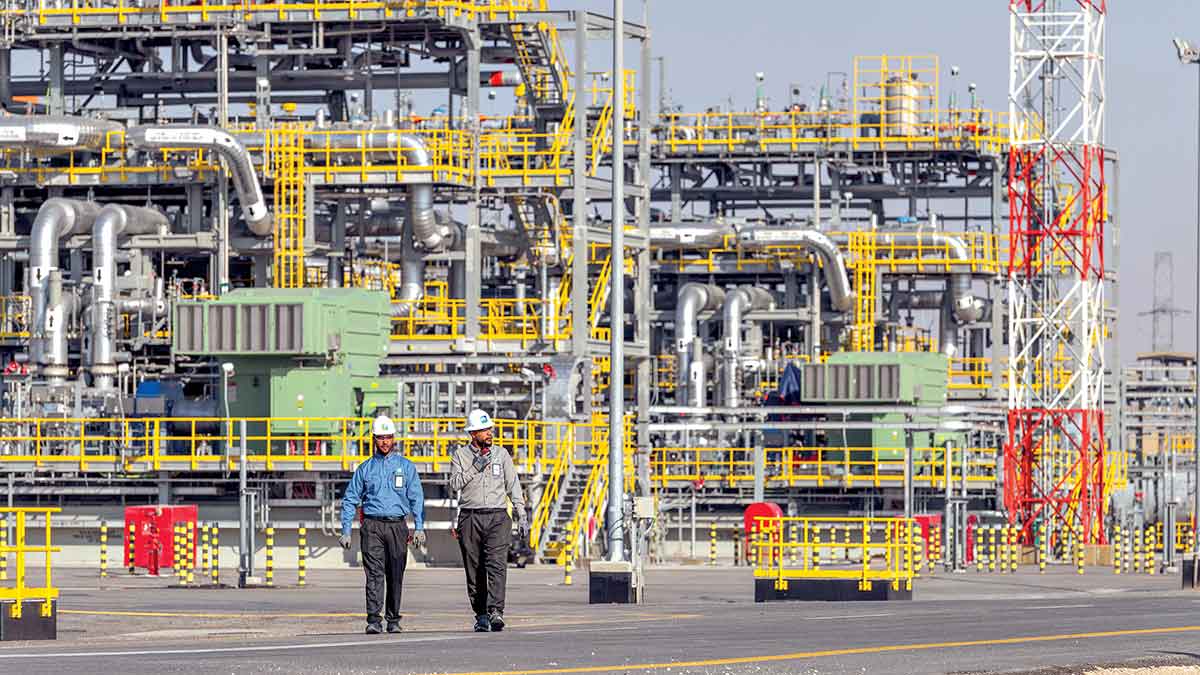
Global July 30, 2023 - By
The Aramco investment is key toward the nation’s plan to diversify its energy mix by cutting its use of crude oil and liquids for power generation.
An extensive Aramco integrated investment is expected to add an impressive 20 production years to three nonassociated gas reservoirs lying within the world’s biggest onshore oil field, Ghawar, and 15 surrounding fields.
Located in Saudi Arabia’s arid eastern desert region, the highly-innovative development known as “Haradh and Hawiyah Increment” extends across an area the size of a small country, and is raising the Kingdom’s daily gas production by an immense 1,360 million standard cubic feet per day (MMscfd).
The Aramco investment is key toward the nation’s plan to diversify its energy mix by cutting its use of crude oil and liquids for power generation. It also builds on the company’s strategy to produce valuable feedstock for the petrochemical industry.
Upstream’s ambition to double gas production by the end of this decade reflects our dedication to solving the energy trilemma, and facilitating an orderly and equitable energy transition, while continuing to provide a reliable supply of affordable, reduced carbon-intensity fossil fuels to the Kingdom and beyond.
— Nasir K. Al-Naimi, president, Upstream
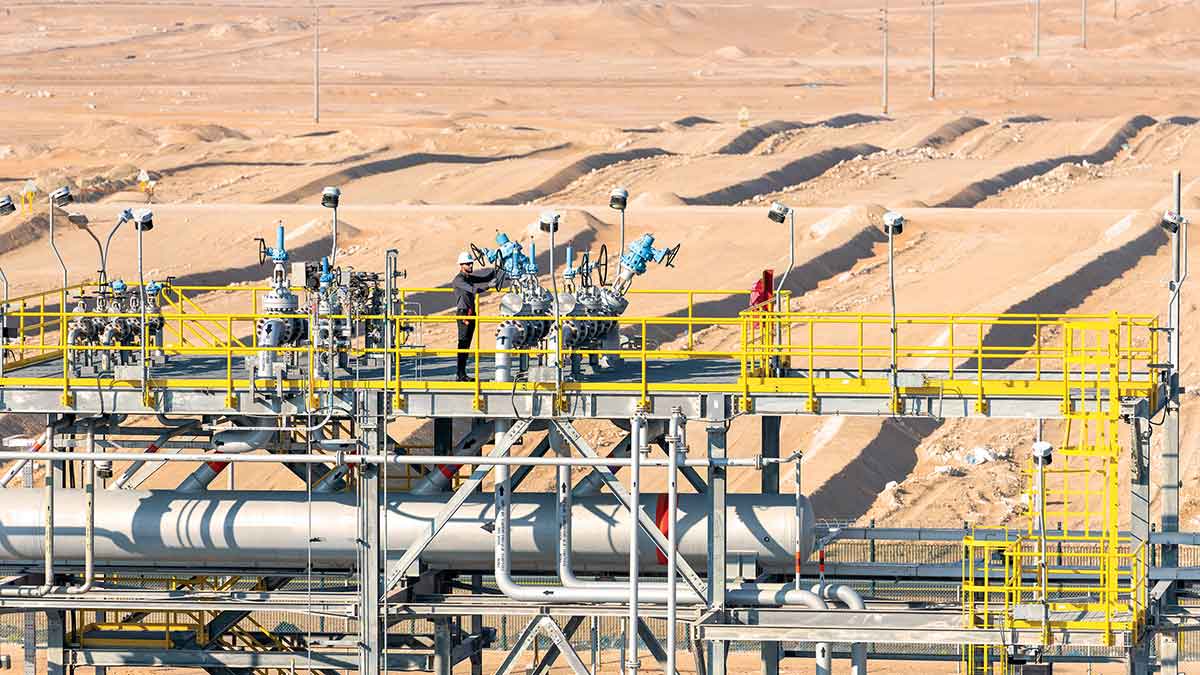
Three major elements
Running across multiple sites, the intricate expansion above 15 fields and three reservoirs has dispensed nine new compression plants across 30,000 km2, increased gas plant processing capacity at Hawiyah by nearly one-third, and added to deep ethane recovery at ‘Uthmaniyah.
Despite challenges such as remoteness and COVID-19, Saudization and innovation have been major features of the project.
Innovating acceptance testing
Completed during the challenges of COVID-19, the pandemic introduced fresh thinking to the compression projects.
For the first time, Aramco switched to remote factory acceptance testing, which saw company engineers work from home to confirm readiness of the compression plants’ process control systems to project specifications and company standards.
Multi-disciplinary teams formed for the preservation program had contractors and vendors working together to track the equipment journey from arrival to site, until implementation of preservation requirements, and an integrated project team developed a robust preservation program to ensure integrity of assets already delivered to site.
In another first for Aramco facilities, 54 maintenance-free multi-cyclone filtration systems were installed upstream each stage of gas compression to — across a range of operating conditions — use centrifugal force to efficiently remove 99% of bulk liquids and solid particles from the gas flow, while achieving minimal pressure drop.
Saving $8 million through innovation at Hawiyah
To maintain its gas condensate specification, Hawiyah Gas Plant (HGP) innovated installation of the first-of-its-kind liquid-liquid coalescer in the feed drum at stabilizer unit, providing an efficient water/oil separation to meet the water-in-condensate specification of the stabilized condensate of less than 20 ppmv, and avoiding spending $8 million on installing a standalone filtration system.
Recalculating flow equation to low pressure
Underground oil and gas is not a calm lake of fluid. Instead, like honey in a sponge, it hides in multiple porous underground rock spaces, known as reservoirs.
When a nonassociated gas reservoir begins to reach its plateau, its natural pressure decreases, and to both improve and continue production of lower-pressure gas, wellhead pressure is lowered. After gas reaches a wellhead, it passes through a choke valve for correction to normal operating pressure, and control of its flow rate.
To produce lower pressure gas from the Khuff, Jauf, and Unayzah reservoirs, firstly the choke valve for more than 1,000 wellheads was reduced to 300 pounds per square inch (psi). Secondly, to bring the pressure of this same gas up to the level required for an Aramco gas plant, the gas needed to be compressed to 550-600 psi.
Three-phase separation
Increasing gas pressure is the job of a compression plant. In a first-of-its-kind configuration for Aramco, the development has scattered nine identical-looking compression plants to the far corners of the rose-gold desert sands on the surface of the three reservoirs.
Low-pressure gas from the reservoirs is both sour — containing hydrogen sulfide— and sweet.
Processing trains in the compression plants also do three-phase separation; instead of using typical gravitation force for separation, the compression plants use centrifugal force to remove condensate and water before compressing the gas.
Once compressed, the high-pressure gas travels through underground pipelines from six compression plants to HGP for final processing, while the remaining three plants dispatch to Haradh Gas Plant (HdGP).
Condensate travels through 6 to 14 inch nonmetallic pipelines to HGP and HdGP for onward processing in Abqaiq, while three compression plants send produced water to HGP, one plant sends to HdGP, and the remaining five place the water into water injection wells.
Our Capital Expenditure Program
Aramco has embarked upon the largest capital expenditure program in its history, growing our 2022 capex by 18.0% to reach $37.6 billion.
Why? Because we anticipate oil and gas shall remain essential for the foreseeable future.
We intend to maintain our position as the world’s largest crude oil company by production volume as well as one of the lowest-cost producers.
Our significant energy expansion plans are on track, and include doubling our gas production by 2030 to meet growing demand for lower carbon energy and additional liquid volume for export, as well as supporting our future potential to build a hydrogen value chain, and be active in the export of blue ammonia.
An important auxiliary benefit of Aramco’s gas production is the significant NGL and condensate yields, which supplement crude oil production and provide much needed feedstock to the refining and petrochemical industries.
Decentralized digital eye
Data on Aramco plants provides a helping hand to enhance safety, efficiency, and mitigate greenhouse gas (GHG) emissions. Sophisticated process controls keep a finger on the production pulse by integrating real-time data into the production processes.
Changing to lower-pressure gas production has meant decentralizing part of the Supervisory Control and Data Acquisition (SCADA) systems from Hawiyah and Haradh plants to the compression plants. Each compression plant has its own control room, a centralized electronic nerve center where advanced algorithms keep an eye on end-to-end operations.
To suit lower pressure 300 psi production, wellhead instrumentation, and associated transmission lines, required adjustment.
Kingdom’s largest gas plant
Situated about 60 km south of the ancient oasis region of al-Hasa, HGP’s collective aim is to remove water, hydrocarbon condensate, carbon dioxide, and hydrogen sulfide from raw gas, and turn it into sales gas suitable for sending to the Master Gas System (MGS). The plant, becoming operational in December 2001, was Aramco’s first facility to process nonassociated gas directly from a reservoir.
Processing an additional 1,360 MMscfd of raw gas requires corresponding processing infrastructure. HGP’s 1,070 MMscfd increment has transformed it into the Kingdom’s largest gas plant.
Originally designed to process 1.6 Bscfd of raw nonassociated gas to produce 1.4 Bscfd of sales gas, and 170,000 barrels per day of condensate, HGP was expanded in 2009 to increase its capacity to 2.6 Bscfd and 240,000 barrels per day.
Ghawar’s gas production increase, however, has grown the plant’s capacity to a massive 3.5 Bscfd, with two sparkling new treatment trains on the eastern border joining the plant’s five existing trains.
Improved HGP industrial processes
With the increment has come a number of opportunities for production improvements, bringing associated benefits of higher levels of environmental mitigation. Standouts are better use of steam, and flare gas prevention through improved recovery.
Vigilant control over excessive gas pressure variations protects industrial facilities, the people working there, and the environment. Burning gas, known as flaring, is a safe control mechanism but is also wasteful.
HGP’s flare system, likewise situated on the southern border, has welcomed the significant addition of a new flare gas recovery system. The system both recovers and repurposes gas that would have previously been flared.
A blowdown liquid recovery system, discretely hidden behind adjacent storage tanks, collects and recovers flared liquids, which provides additional flare prevention. Reducing routine flaring supports Aramco’s participation in the World Bank’s Zero Routine Flaring by 2030 initiative.
Steam, from process heating to fractional distillation, is a backbone to both oil and gas processing, and high-pressure steam was controlled at HGP by a let-down station. A new steam turbine generator now converts this steam into 37 megawatts of power, which is used to both run the plant’s units, with any excess exported to the Kingdom’s power grid, adding to the electricity already exported by the plant’s existing two cogeneration units.
Valuable natural gas byproduct
Operating adjacent to Hawiyah gas plant is the downstream Hawiyah natural gas liquids recovery plant (HNGL), while within the area is the ‘Uthmaniyah Gas Plant (UGP). Natural gas liquids (NGL), highly valued components of natural gas, have a wide range of applications, such as specialized fuels, fertilizers, and petrochemical feedstocks.
Ethane is an important feedstock for the petrochemicals industry, and the Kingdom has an ethane supply-demand gap. Included in the development was a deep ethane recovery system at UGP.
While existing HGP dry sweet gas is sent to HNGL for NGL extraction, the increment gas is sent to UGP for deep ethane recovery through a new 56-inch pipeline.
844-kilometer nonmetallic pipeline deployment
Working with lower-pressure gas requires more horsepower, and more pipelines. Both have to be designed and tested for low-pressure functionality.
Upgrading the Ghawar reservoir’s existing gas gathering pipeline network to low-pressure operational mode has seen one of the largest deployments of nonmetallic pipelines in Aramco.
A total of 2,718 km of different sizes and types of metallic and nonmetallic flow, trunk, transmission lines have been laid to transport nonassociated gas, condensate, and produced water.
All 844 km of the liquid pipelines — condensate and produced water – are nonmetallic.
Extending the Life of Our Fields
To meet growing domestic gas and NGL needs, Aramco’s significant gas development and increment investment at Haradh, Hawiyah, and ‘Uthmaniyah is estimated to have extended the plateau life of 15 fields by 20 years.
Gas gathering infrastructure
• 866 wellheads modified
• 9 new remote headers (new total 59)
• 1 gas gathering manifold (new total 6)
9 gas compression plants
• 6 Hawiyah
• 3 Haradh
• 7 liquid separation stations
2,700 kilometers of pipelines
• flow
• trunk
• condensate
• water
• transmission combined condensate and produced water
Caption for top photo: The Aramco investment is key toward the nation’s plan to diversify its use of crude oil and liquids for power generation. It also builds on the company’s strategy to produce valuable feedstock for the petrochemical industry.