Fighting Flaring
Better for business, better for the environment: Avoiding the need to flare during NGL train start-up
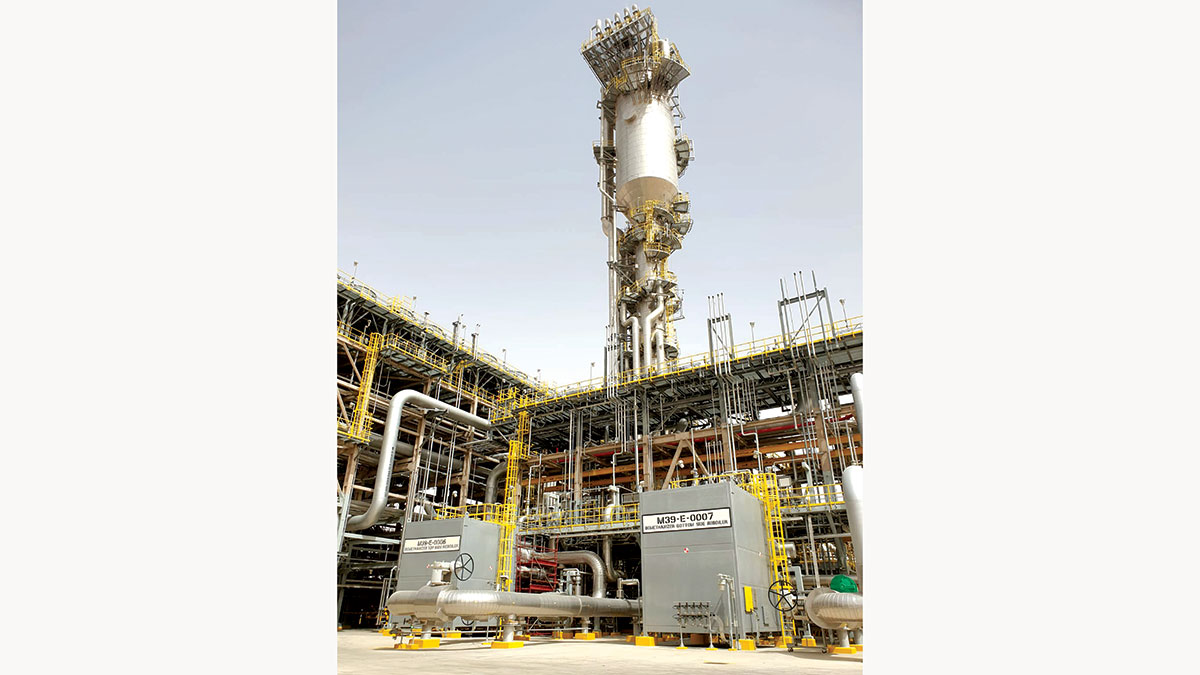
Global July 26, 2022 - By
Gas plant eliminates 600 million standard cubic feet of gas flared during maintenance process for natural gas liquids train.
Spectacular achievements result when we combine our innovative thinking with Aramco’s decades of maintenance experience.
Pioneering work from the team at the ‘Uthmaniyah Gas Plant has avoided the need to flare approximately 600 million standard cubic feet (MMscf) of gas during the final maintenance process for a natural gas liquids (NGL) train. During the final testing and inspection (T&I) of an NGL train, gas is customarily flared at its start-up to dry out the infrastructure.
As highly valued components of natural gas, NGLs are key raw materials for chemicals, plastics production and vehicle fuel blends, and the core purpose of an NGL train is to convert natural gas to NGL.
Maintenance safety and environmental critical
Keeping equipment and systems at their top readiness is not only best for business continuity, but paramount toward mitigating against environmental impacts, and Aramco invests in maintaining the company’s extensive portfolio of assets.
Maintenance of NGL trains is critical toward employee safety, process control, and environmental protection.
— Fahad S. Dossary, ’Uthmaniyah Gas Plant Department manager
“During a train’s maintenance, moisture builds up from hydrotesting, and other maintenance activities,” Dossary said. “It is common practice to send the gas used to dry out the train to the flare stack.”
Instead of flaring the gas, ‘Uthmaniyah added piping modifications and valves to an ethane train, allowing most of the gas to be recovered instead of flared. This approach was unprecedented for this type of natural gas processing process, and required expert evaluation and analysis before implementation.
“We dried out the maintained train by flowing the gas through, allowing it to pick up the moisture, then compressed the gas through our existing compressors, and sent it back to the plant inlet pipe,” added Dossary.
“Instead of wasting the gas, we safely recovered it, striving to reduce our energy use, and our greenhouse gas emissions.”
Engineering lower carbon footprint
Engineering superintendent Shadi M. Hazmi explained the previous practice of flaring approximately 600 MMscf of gas was part of the T&I dry out and start-up procedure, required to remove water moisture from the unit piping and equipment.
“When processing gas, the NGL unit drops the temperature of the gas to approximately 100 degrees below the freezing temperature of water, therefore, the need to remove water moisture, and the necessity of flaring,” said Hazmi.
During the design phase of ‘Uthmaniyah’s new Ethane Recovery project, our engineers came up with an innovation to modify the structure of the pipes so that a new path is added to capture the gas used in the drying process.
— Shadi M. Hazmi
“We presented the idea to experts to evaluate, study risks and assess the prospect of going forward with implementation, and it was incorporated in the unit’s engineering designs. The idea was successfully put to the test during the unit’s commissioning and eliminated the need for flaring during the dry out procedure,” said Hazmi.
Aramco is committed to the World Bank’s Zero Routine Flaring by 2030 initiative, and other company NGL plants are looking at the feasibility of applying the same approach for their NGL trains.
First WEF Lighthouse facility
The ‘Uthmaniyah Gas Plant, commissioned in 1981 as part of the Master Gas System to process associated gas from oil wells, is one of the world’s largest gas processing plants, and operates four NGL trains.
Four years ago, the ‘Uthmaniyah Gas Plant became the first oil and gas plant in the world to be designated a Lighthouse by the World Economic Forum for its pioneering adoption and integration of cutting-edge technologies of the Fourth Industrial Revolution (IR 4.0).
Aramco, the only international energy company to be recognized by the Forum’s elite group of IR 4.0 pioneers, has also achieved Lighthouse status for its Khurais and Abqaiq facilities.