Automation and Ingenuity
Aramco’s Spare Parts Reverse Engineering initiative looks to drive savings, efficiency
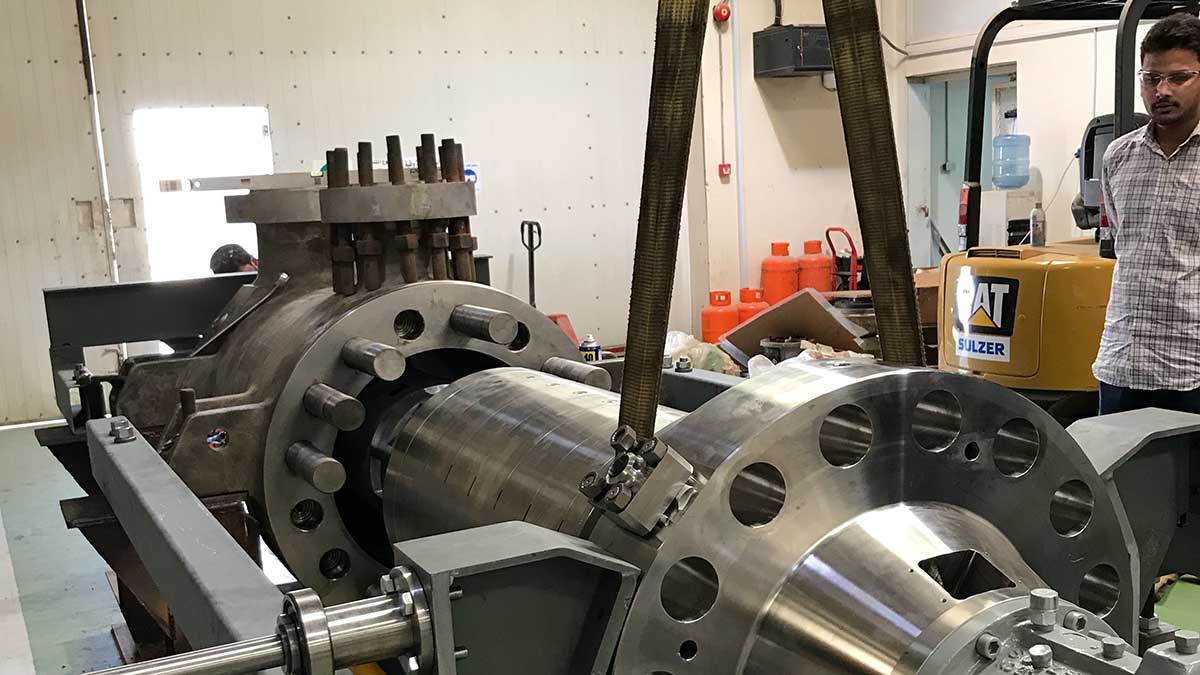
Global November 03, 2021
The initiative is intended only for parts that are neither protected by intellectual property rights nor any contractual obligations.
Aramco’s Consulting Services Department (CSD), looking to offers corporate facilities an alternative for obtaining spare parts, has launched the reverse engineering initiative.
In many cases, reverse engineering provides faster delivery of spare parts for a lower cost. In addition, it enables localization of the engineering and manufacturing of these spare parts. Since its debut, the initiative has targeted approximately 5,500 spare parts and developed more than 600 parts — along with their digital drawings.
A new SAP system enhancement, which was developed specifically for this initiative, was recently launched in a live-streamed workshop organized by CSD and attended by more than 200 participants from different company organizations.
The enhancement provides plant maintenance an additional supply option to order reverse engineered spare parts along with the default supply from the original equipment manufacturer (OEM). The process automation is one of the initiative’s main milestones introduced by CSD in partnership with the Mechanical Services Shops Department, Procurement and Supply Chain Management and the Inspection Department.
The initiative targets spare parts that are either obsolete, costly or have long delivery lead times.
Benefits of reverse engineering
This alternative process will definitely improve business continuity and reduce overall equipment ownership cost. In addition, it will create a healthy competition between OEMs and the local qualified reverse-engineering vendors to improve delivery and reduce cost, as well as create better opportunities for local content growth.
Reverse engineering and its techniques have revolutionized the way we maintain our operations, and several company’s plants have already benefited from adopting it. The Riyadh Refinery, Berri Gas Plant, and Khurais Producing are recent examples where they utilized reverse engineering to resolve obsolescence, high cost, and long delivery lead time.
Riyadh Refinery managed to successfully reproduce a failed crude loading pump impeller through a local reverse engineering process, which resulted in a 75% cost reduction from the OEM cost, and a lead time cut from 6 months to only 6 weeks.
In another instance, Berri Gas Plant reverse engineered an obsolete pinion gear for a gas turbine auxiliary gearbox. The piece was produced with upgraded material with a lead time of less than 6 months.
The techniques of reverse engineering were also applied successfully in the Khurais Producing Department to upgrade 15 saltwater disposal pumps to meet an anticipated demand increase of 140% of the original flow requirement. The retrofit project resulted in a 4% efficiency improvement compared to the OEM original design, and a significant cost savings of approximately 50% by enabling competitive commercial offerings.
Disclaimer: The spare parts reverse engineering initiative is only intended for parts that are neither protected by intellectual property rights nor any contractual obligations.