Shaybah EMSR
Shaybah Executive Management Safety Review: Mitigating risks in the Empty Quarter
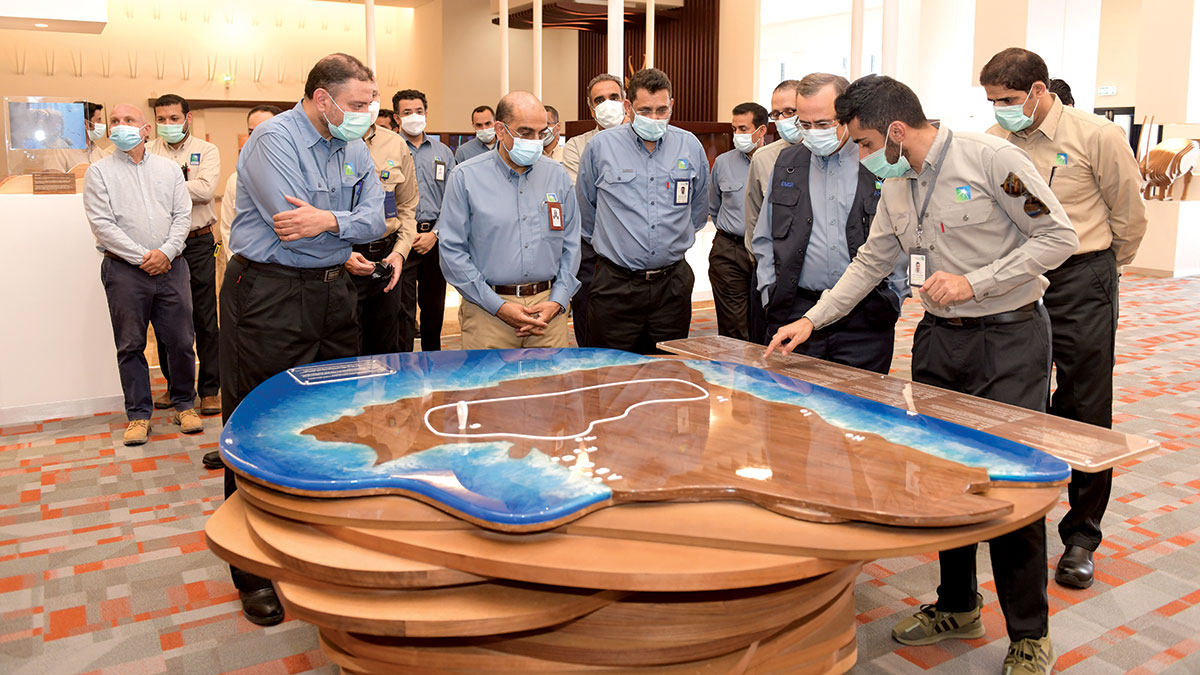
Global September 14, 2021 - By
In the heart of the desert, Aramco drives for safety and environmental excellence.
Aramco president and CEO Amin Nasser traveled to the Shaybah area on Monday, Sept. 13, and was joined by other members of corporate and senior management for the monthly Executive Management Safety Review (EMSR). The tours included visits to the Shaybah NGL plants (SNGL), the Shaybah Producing Department (SyPD), Gas-Oil Separation Plant (GOSP)-2, and the Shaybah Security Project.
The tour also included an inauguration ceremony for the newly constructed Shaybah Wildlife Sanctuary Visitor Center.
The visiting team was presented with Shaybah Area’s safety performance, where the operating departments, in addition to all support organizations, achieved very commendable performance. All safety and environmental indicators presented showed significant improvement compared to previous years and corporate averages.
Mitigating maintenance risks
Visiting the Shaybah NGL plant, the opening safety moment, led by field compliance coordinator Zain O. Omran, highlighted the enhancements made to Isolation, Blinding and Torqueing.
Next, process engineer Mohammed A. Rumaih presented SNGL’s efforts to improve its environment protection program, and included steps to minimize greenhouse emissions, the deployment of circular economy principles to minimize generated waste, and the reclamation of hazardous chemicals.
The tour also heard a presentation highlighting SNGL’s emergency preparedness. Abdullah M Arjani, OE&CG Group leader, showcased the changes deployed on the Firewater System to increase its capacity by 25% and an initiative to improve the Pre-Incident Planning.
Following the presentations, the CEO and accompanying management undertook a facility tour, and included a presentation by Mubarak Z. Alkhaldi demonstrating SNGL's efforts to enhance the reliability of Hazard Gas Detection to improve overall Cogen safety and reliability and detector relocation from elevated locations to mitigate maintenance risks.
Additional presentations by Saud M. Alkabuli explained SNGL efforts to enhance electrical power network reliability. and safety focusing on GIS breaker modification project and surge arrestor installation project to protect the electrical equipment from any power interruption impact. It also includes the Layer-3 network upgrade project to enhance communication cybersecurity. Process Engineer Sultan A. Alankari also showed the performance enhancement of the Brazed Aluminum Heat Exchanger, improving the plant’s efficiency.
Finally, Ahmad M. Seoud, engineering process supervisor, showcased the departments journey to safely install major equipment including Core-in-Kettle and Refringent Fin Fan Coolers.
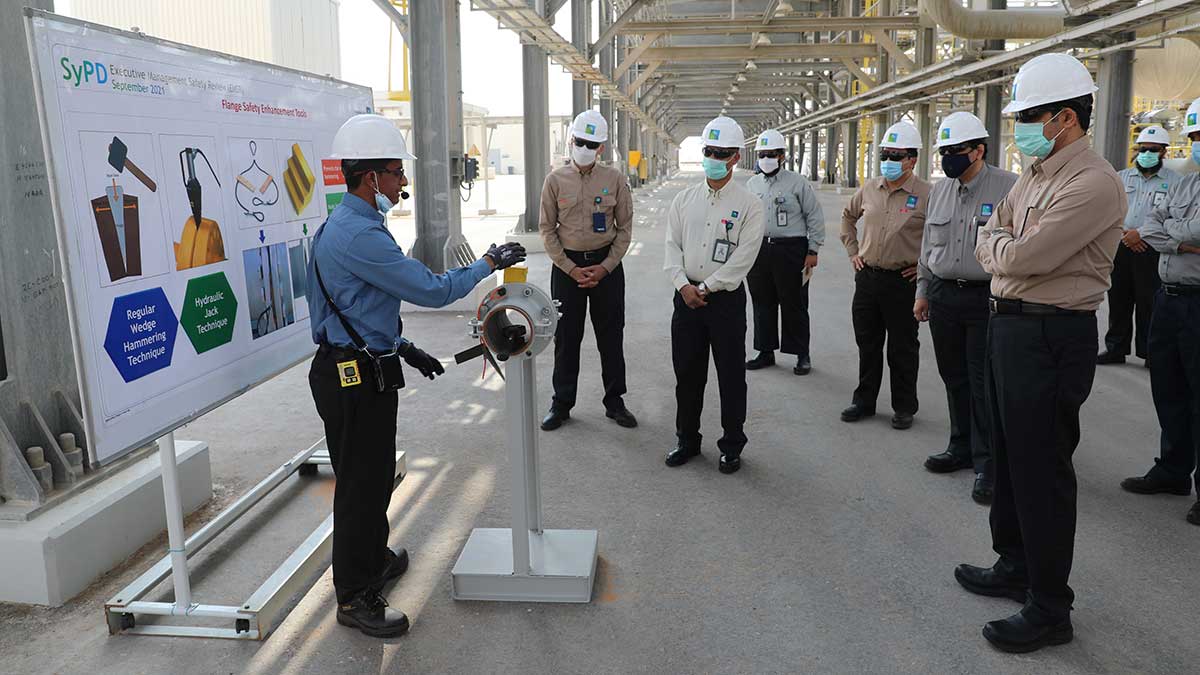
Safety and environmental intiatives
Management also toured the GOSP-2 facilities and were presented with multiple safety and environmental initiatives. Maintenance machinist Abdullah Al-Abood presented on the Bearing Lock and Fin-Fan Shaft Safety Removal Tools. “Removing the lower bearing from the fin-fan coolers is one of the most challenging tasks that takes a minimum of 6 hours to complete with at least three technicians working together using a crane and riggers to secure the shaft in place,” he said.
“To overcome these challenges, we came up with the Bearing Lock Removal Tool, which was fabricated in-house and used to remove bearing lock sleeves safely. In addition, we also designed and fabricated a fin-fan shaft lifter tool,” Al-Abood said.
Al-Abood highlighted that the new tool prevents hand crush and trap-in hazards, among other safety benefits, and the tool has been submitted as a patent and for “Best Practice” recognition.
On the second stop, Hisham Bamansour, a field metal technician, presented on “Flange Safety Enhancement Tools” that were introduced to address the safety hazards that can emerge in the course of metal crews using either a wedge hammering technique or a hydraulic jack to deal with flange breakages. These hazards can include the risk of strike injuries from a flying wedge and crush injuries.
Bamansour said: “The SyPD Maintenance crew improvised a practical solution to wedge hammering by fabricating a wedge that includes tether lines. The tether lines can be connected to any fixed bolt and this will provide protection against wedge fly-out. In addition, we fabricated the Flange Safety Stopper tool that can be placed in the opening between the two flanges to prevent them from crushing. Like the Bearing Lock Removal Tool, this tool has also been submitted as a patent and for Best Practice recognition.”
Harnessing IR 4.0 technologies
In addition to tools that enhance safety, the SyPD also highlighted how they are harnessing the promise of IR 4.0 technologies to bring environmental benefits. Instrument technician Mousa Z. Alkhabbaz shared an initiative to enhance the effective utilization of 3-D printing technology. Used to print spare parts for obsolete critical safety equipment, the deployment of the technology is a testament to SyPD’s journey to implement the department’s IR 4.0 strategy.
The first of two products showcased was the Portable RTD Simulator/Diagnostic Tool.
“This new device can be used at the site without the need for any special tools, and can provide accurate readings that will help the crew troubleshoot the temperature sensing element which minimizes the downtime of critical equipment,” said Alkhabbaz.
The second product showcased was the Vibration Sensor Cable Protection Sleeve, which offers environmental benefits. The new sleeve parts were 3D printed and successfully installed on the vibration sensor cable to prevent grounding of the vibration sensor and avoid trips of major pumps and compressors, preventing excessive gas flaring, improving plant reliability, and preserving the environment.
On the final stop, Haider A. Alrumaih, process engineer at GOSP-2 explained SyPD Environmental Protection initiatives where the department achieved major reduction in flaring through multiple initiatives implemented in-house that resulted in minimizing flaring by more than 20%.
Nasser thanked department personnel for their efforts being translated into an excellent safety record, and he highlighted the ongoing importance of safety across all business lines, particularly in the context of the many new industrial projects that lie ahead.
TOP PHOTO
During the visit, the Shaybah Wildlife Sanctuary newly constructed Visitor Center was officially inaugurated by Aramco president and CEO Amin Nasser. The purpose of the center is to host visitors and provide an inspirational venue to educate and inspire on the wonders of Arabian wildlife and also showcase the corporate environmental profile.