Global April 12, 2021
New type of testing improves quality and speed in addition to being safer.
The Inspection Department has successfully field-tested digital radiography technology to test project welding safety.
The first digital tests of welding quality and integrity were performed at the Haradh and Hawiyah gas production plants on the giant Ghawar field, and pave the way for a planned companywide rollout to replace conventional testing by 2023.
Digitizing industrial radiography testing vastly improves image quality and process speed, and does away with hazardous chemicals, dedicated dark rooms, lengthy transportation, and specialized storage facilities.
Under the new two-minute process, digital detectors automatically produce a high-quality electronic image. This can be scanned and displayed on any digital monitor, sent over the internet, and stored on the cloud or memory sticks. It can also be printed, if necessary, using reusable film.
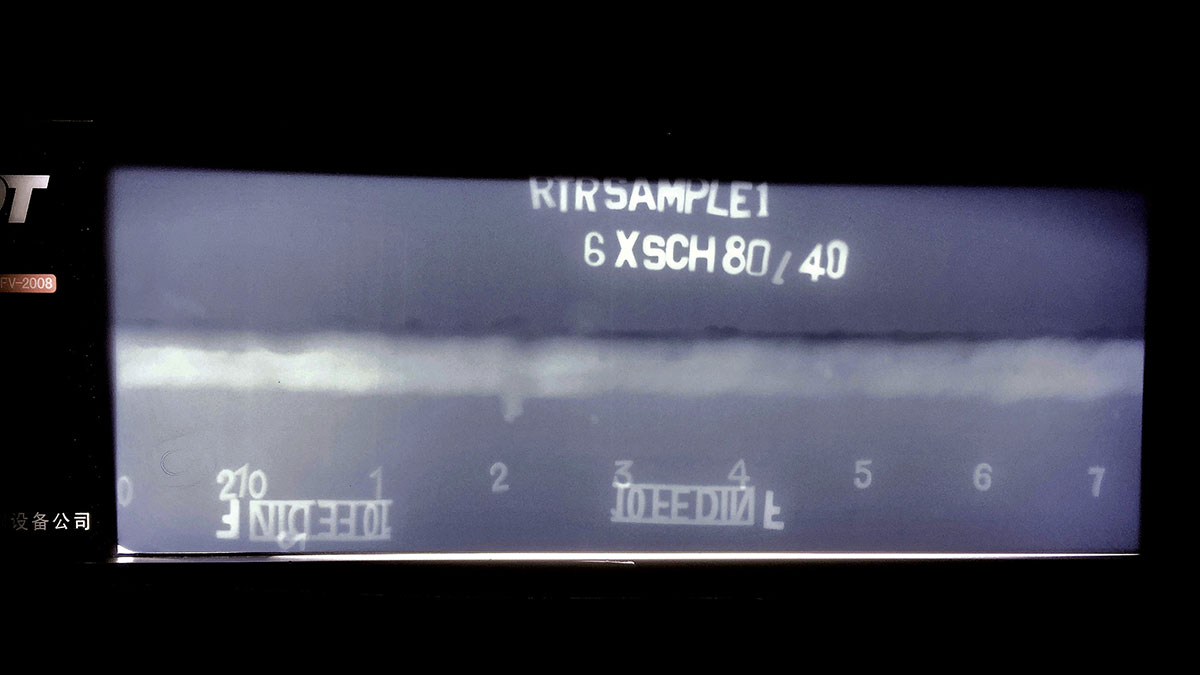
Previously, manual radiography testing was a lengthy 30-minute process that involved using special equipment with chemicals and darkroom technology to extract a lower quality paper image, akin to analog photography. After extraction, the picture was interpreted to assess the weld quality.
This manual process was time-consuming, often resulting in backlogs and project delays, partly as a result of transportation and storage of sensitive films in climate-controlled facilities.
The main objective of project inspection is to ensure quality. Projects have significant welding operations on-site or at fabrication shops. Using X-rays or gamma rays to see through the welds automatically ensures the joints meet standard acceptance criteria for safe and reliable operation.
The successful deployment was the result of collaboration between the Inspection Department, the Gas Compression Project Department, Spanish-based contractor Técnicas Reunidas, local construction contractor Nasser S. Al Hajri Corporation, and a local nondestructive technologies (NDT) service provider, the NDT Corrosion Control Services Company.
Toward a circular economy
Circular economy is essentially the conservation and reuse of materials. Instead of making, using, and then disposing of materials, circular economy tries to keep resources in use for as long as possible by extending their life and then recycling them into something else.
Once digital radiography technology is rolled out to all Aramco projects and operating facilities by 2023, it will result in the elimination of the production of millions of hardcopies of conventional films and climate-controlled storage facilities, replacing them with digital images stored on a cloud server. The technology will also have a positive environmental impact by eliminating the use of thousands of gallons of processing chemicals.
Bader A. Busbait, manager of the Inspection Department, said digital radiography was only the first step for the department’s digital transformation.
“There are numerous other inspection programs, services, and techniques that have great potential for digitization and optimization that will be implemented in the near future,” he said.
“This will ultimately support Aramco’s circular economy.”