Corrosion and Nonmetallics
Engineers bridge gulf between 3-D printing, nonmetals to solve seawater corrosion
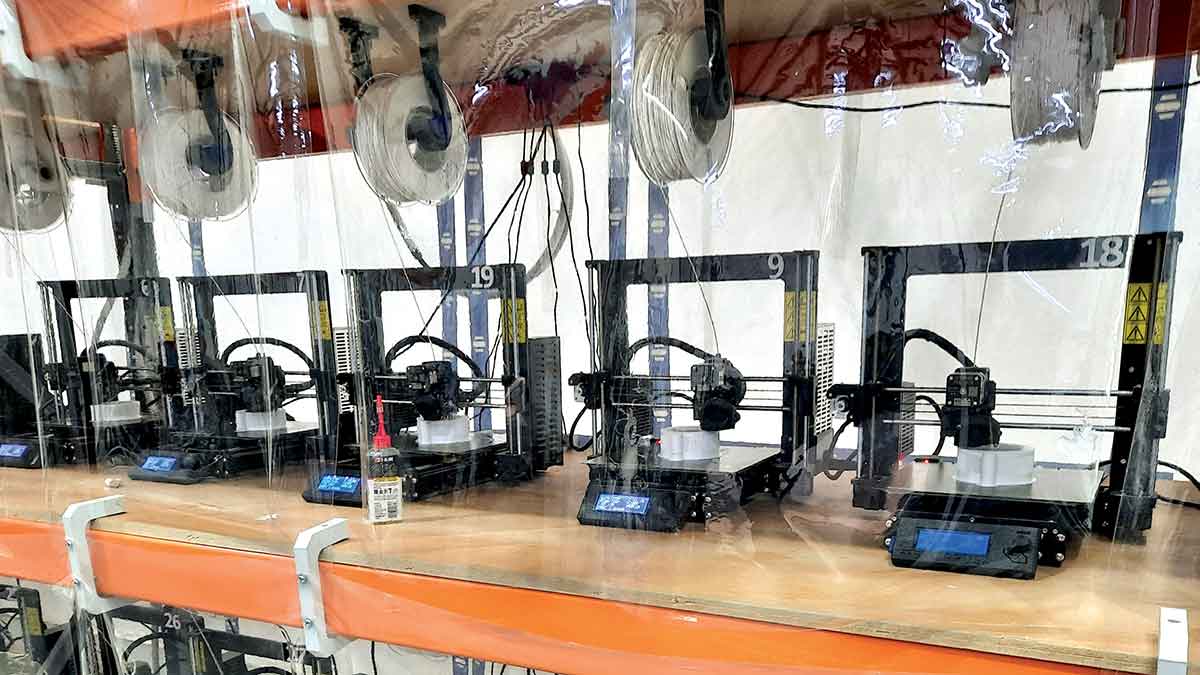
Global April 11, 2021
The Consulting Services Department solution could provide big savings in the coming years.
After years of scratching their heads, engineers with the Consulting Services Department (CSD) have finally solved a longstanding seawater corrosion problem by combining nonmetal materials and 3-D printing, potentially providing the company significant savings over the next 20 years.
The problem lay in the filtration system at the Qurayyah Sea Water Treatment Plant, where corrosion in the internal piping of sand filters and laterals — tiny horizontal side pipes in the system — meant sand was getting into the seawater injection network.
This sand intrusion affected the operation of the filter and the corrosion inhibition system, leading to frequent shutdowns to repair the leaks.
Conventional nonmetallic production technologies were unable to produce the required lateral, or side slit spacing, which is measured in micrometers, a millionth of a meter and tiny in scale.
Lateral thinking
Nonmetallic materials with their corrosion resistant properties, functionality, and versatility are becoming the material of choice for different applications. 3-D printing utilizing nonmetallic materials allow unique designs and offer a flexibility that is impractical or impossible with traditional methods.
The solution was a blend of polycarbonate and acrylonitrile butadiene styrene polymeric material suitable for 3-D printing and mechanically compatible with the corrosive service conditions of the seawater filtration system.
The engineers were able to 3-D print nonmetallic laterals with micro slot holes of 150 microns. In comparison, a human hair has a diameter of between 40 to 90 microns.
After precisely reverse engineering the steel laterals, a 3-D model was created and analyzed using finite element analysis for structural stability verification.
Huge savings
The prototype was dimensionally checked and fluid flow parameters were compared with the metallic laterals by performing flow assurance testing.
Upon successful completion of the engineering phase, 90 laterals were 3-D printed using 20 printers at a local vendor facility.
The excellent corrosion resistance capability of the nonmetallic material coupled with 3-D printing technology is expected to give the most cost-effective method of producing laterals.
Mass deployment of this technology in the remaining sand filters will provide at least 20 years of service life with an expected cost saving of more than $16 million.
Patently clear
This collaborative effort between the Sea Water Injection Department and CSD also resulted in intellectual property protection in the form of a patent in the United States Patent and Trademark Office.
Aramco’s in-house 3-D printing capabilities are being enhanced to enable printing of the remaining required laterals for the plant. This initiative will pave the way for more deployment opportunities of this patented design and commercialization of the technology internationally.
The plant at Qurayyah, on the Arabian Gulf, treats seawater, which is then piped to the southern fields where it is injected into the ground to help force oil to the surface. The injected seawater replaces the oil extracted from the reservoir.
This innovative idea of combining the state-of-the-art additive manufacturing 3-D printing technology with nonmetallic materials has addressed a chronic field corrosion challenge and yielded substantial life cycle cost savings.