OPERATIONS
Marjan Offshore Gas Project saves money, steel, and space with new flow meter installation
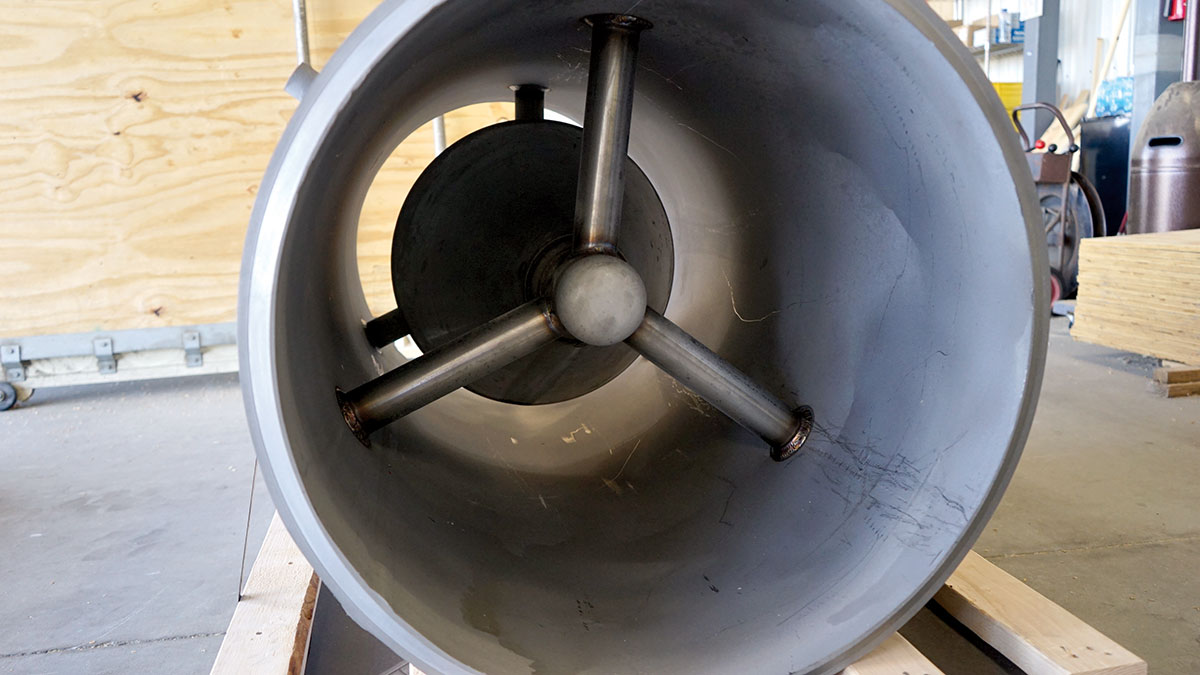
Global March 11, 2021 - By
Cutting-edge technology challenges design norms.
Advanced differential pressure technology is being used for the first time in an offshore application, resulting in a cost savings of millions of dollars at the Marjan Offshore Gas Project.
In line with Aramco’s efforts to optimize capital expenditure and increase technology utilization, the Marjan Offshore Gas Facilities Division (MOGFD) of the Marjan and Zuluf Increment Projects Department has implemented cutting-edge cone flow meter technology.
The in-line devices consist of a cone enclosed in a housing pipe. The cone faces upstream and a pressure difference is read across the device. This difference is then converted into velocity using energy conservation applied to fluid flow, using Bernoulli’s equation, which put simply, adds static pressure to dynamic pressure to produce a measurement of total pressure.
Thinner pipes, less steel
Nabil A. Al Majid, senior project manager with the MOGFD, said the innovation was inspired by the company’s emphasis on reducing capital costs and challenging design norms.
“The project team were successful in identifying this field-proven technology, aligning it with all project stakeholders, and reaping monetary savings and efficiency improvements,” Al Majid said.
The savings come from a reduction in the amount of steel used in the project due to thinner pipe walls. Compared to conventional orifice plates and venture meters — both used to measure flow rate — cone flow meters save approximately 70% of straight piping due to reduced width requirements.
Pipe thickness is reduced from 22D Upstream and 4D Downstream for an orifice plate (in accordance with ISO 5167) to 3D upstream and 2D downstream. The measurement 22D means the radius of the pipe is 22 times the outer diameter of the pipe.
The savings come from a reduction in the amount of steel used in the project due to thinner pipe walls. Compared to conventional orifice plates and venturi meters — both used to measure flow rate — cone flow meters save approximately 70% of straight piping due to reduced width requirements.
Smaller platform footprint
As a result, space on a platform can be reduced significantly, saving more steel on any mezzanine and main deck extensions, including the laydown area; bridge crane gantry rail extensions and strengthening; boat landing extensions from the main deck; and jacket strengthening, including piles.
In addition to space optimization, cone flow meters are relatively easier to install compared to other meters. They also cause a lower pressure drop and have significantly higher accuracy with a lower operating cost. Third-party laboratory calibration ensures the accuracy of meters larger than 20 inches.
The use of the meters serves as a solution for compact offshore platforms and in brown field projects where space is limited. The meters can also be used for cases where high turndown flow measurements are required.
The use of this new technology is reflected in the project’s ongoing design and will be in operation in 2024.
The implementation of cone meters was reviewed and concurred by project stakeholders, including the Process and Control Systems Department, the Production and Facilities Development Department, and the project proponent.
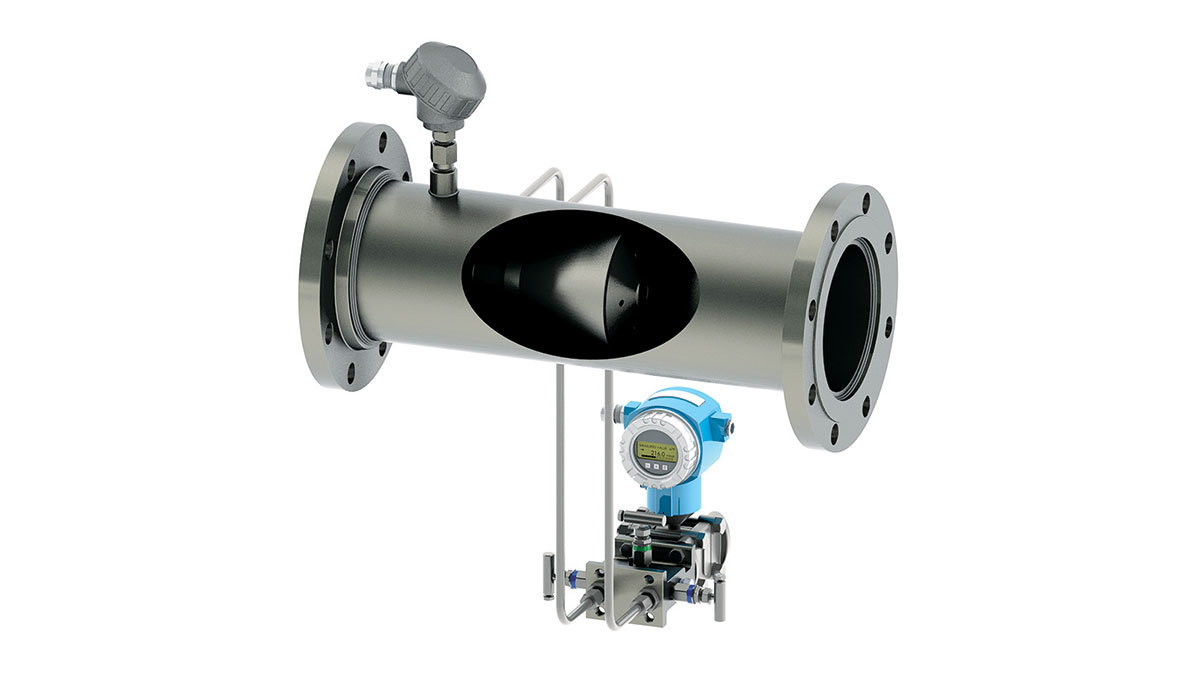