Global January 27, 2021 - By
‘Ain Dar’s five sulfate removal units commence operation.
There are many ways for the natural pressure of an oil and gas reservoir to get a helping hand.
Injecting seawater is one way to assist, but sometimes the ocean’s salt reacts with the underground formation, causing oil and gas production issues.
Scale formation plugs reservoir porosity, impacting production.
Removing the salt before injection — desulfation — solves this, and Aramco recently turned on one of the world’s largest onshore sulfate removal plants at ‘Ain Dar.
Flicking on sulfate switch
In September 2020, on the eastern border of Ghawar, the world’s largest oil and gas reservoir, the company fired up five newly constructed giant sulfate removal units.
Following a January 2018 contract signing and October 2018 commencement, construction of ‘Ain Dar’s sulfate removal plant took 21 months to complete.
The impressive new facility takes power from ‘Ain Dar’s water injection plant to energize its electric motors, and its equipment includes a substation, five nanofiltration trains, four high-pressure water injection pumps, and common utilities.
New construction technology for the project included cost-effective and timesaving polymer for sand stabilization on pipeline berms, and durable lightweight nonmetallic grating.
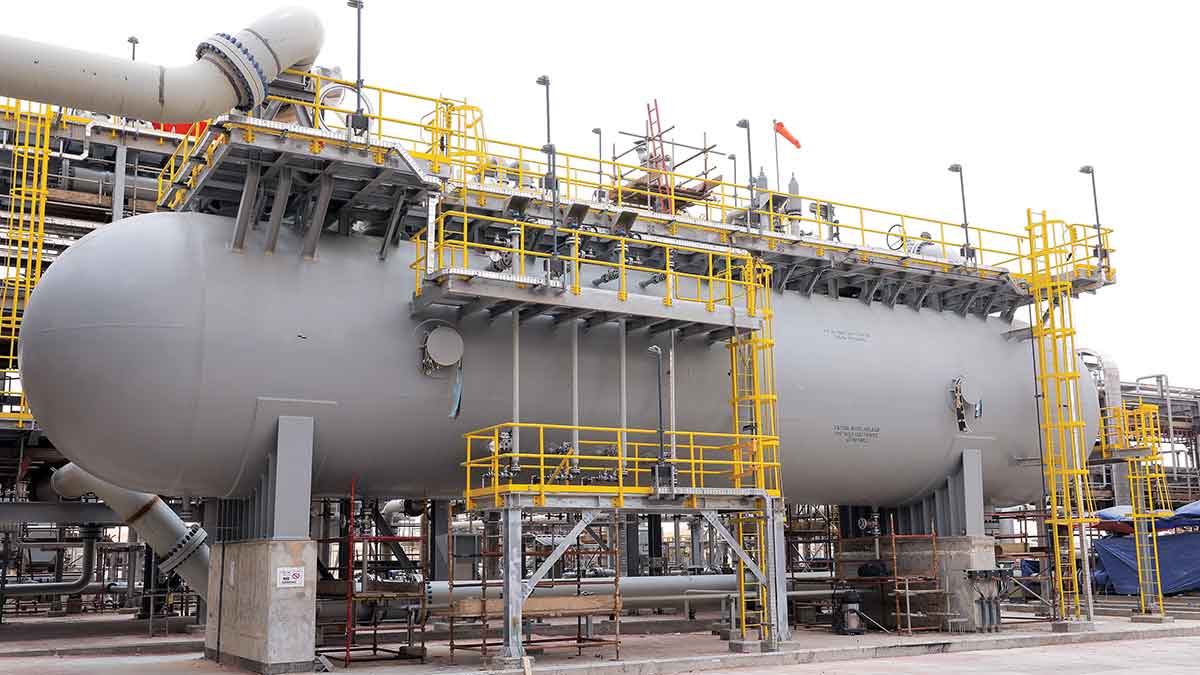
Seawater for enhanced recovery
Ocean waters account for more than 95% of the Earth’s water, and in arid Saudi Arabia, using seawater to enhance oil recovery makes good sense, and contributes to water conservation.
The sulfate removal units supply more than 12,000 gallons of water per minute to be used for enhanced oil recovery.
Through each unit, the 100,000 m2 facility pumps high-pressure Gulf waters piped from Aramco’s Qurayyah seawater plant, across finely membraned filters for injection into Ghawar’s ‘Ain Dar and Fazran fields.
Oil Facilities Projects Department then manager, Ahmed U. Al-Aredhi, said that using desalinated seawater to push oil from a reservoir to a well was a prudent use of the Kingdom’s precious resources.
“Using seawater with reduced sulfate has less impact on operational facilities, which translates to a lower industrial footprint,” said Al-Aredhi.
Getting salt out of water
Making seawater suitable for industrial use involves applying pressure.
Gulf waters are particularly salty, with approximately 57,000 milligrams of salt content per liter, which is higher than most oceans and seas around the world.
The five sulfate removal units use nanomembrane filters for the large-scale removal of salt and impurities, and project engineer Hussain M. Alramadhan says the units’ sophisticated nanofiltration stops almost all sulfate from getting through.
“The units reduce the sulfate in the seawater from 4,400 ppm to less than 200 ppm,” said Al-Aredhi.
The nano-membrane filters remove large dissolved salts — divalent and larger ions, ions with electronic charge of 2 and larger, such as sulfate ions SO4-2, Ca+2, and Mg+2.
Monovalents — small dissolved salts and ions such as Na+1 and Cl-1 — will pass through the filters as they have no impact on reservoir formation.
Khurais multiple stream
Khurais, one of the world’s largest intelligent fields, also recently commissioned a multiple stream seawater reverse osmosis and sulfate removal facility.
Put onstream in August 2020, the first-of-its-kind facility in Aramco is part of an environmental commitment by Khurais to stop the use of non-potable (non-drinkable) groundwater in the processing of crude oil.
Treated through nano-membranes, the low sulfate seawater is injected into the Khurais Lower Fadhli reservoir, enhancing crude oil production by reducing scaling and clogging of the oil reservoir caused by sulfate.
The seawater reverse osmosis and sulfate removal facility at Khurais has 14 trains, producing four streams of water with several ionic compositions, each used for various purposes.
Every drop used
Al-Aredhi said rejected seawater is redirected back to the existing water injection wells, “No drop of the seawater is wasted.
“Although high in sulfate, the rejected water can be used in oil fields whose oil and gas chemistry does not react with the sulfate,” he explained.
Product water from the ‘Ain Dar facility is sent to north Ghawar and lower Fadhli oil reservoirs.
The Kingdom has a small number of large and productive oil reservoirs, low per barrel gas flaring rates, and low water production.
This combination results in less mass lifted per unit of oil produced, less energy used for fluid separation, handling, treatment, and reinjection.
Together, all contribute to the low upstream carbon intensity of Arabian oils.
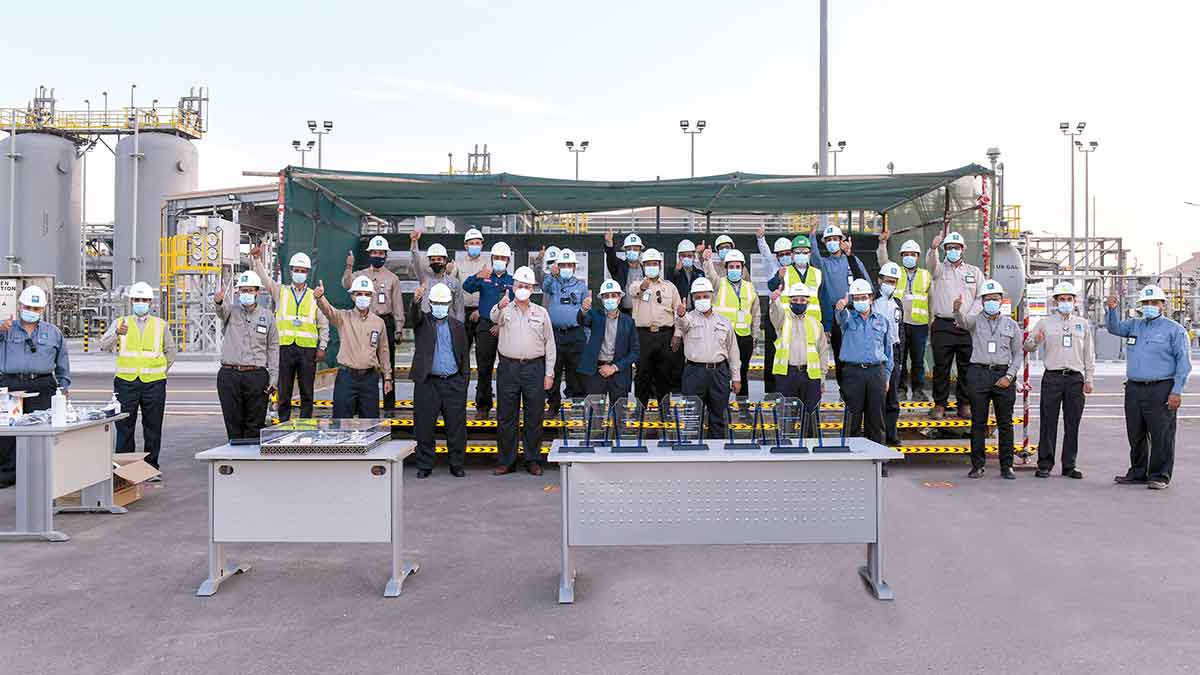